Bamboo Towel
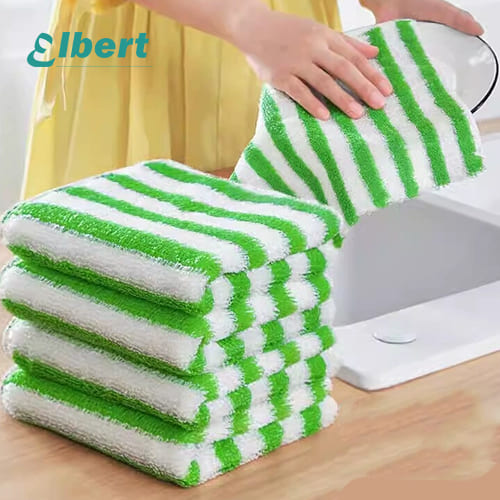
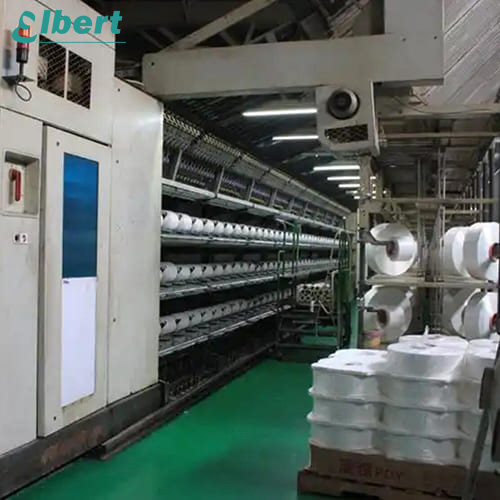
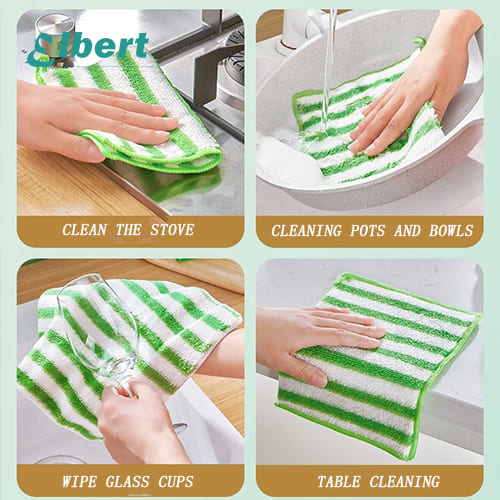
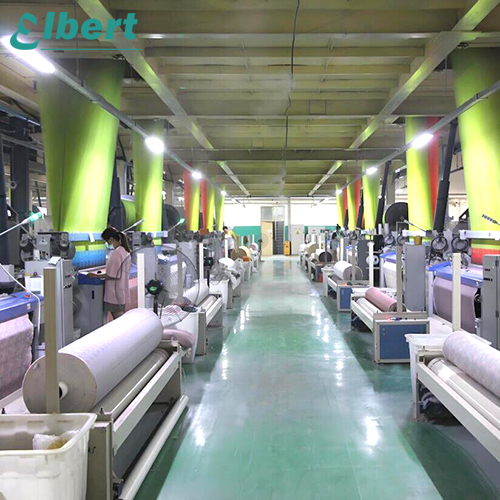
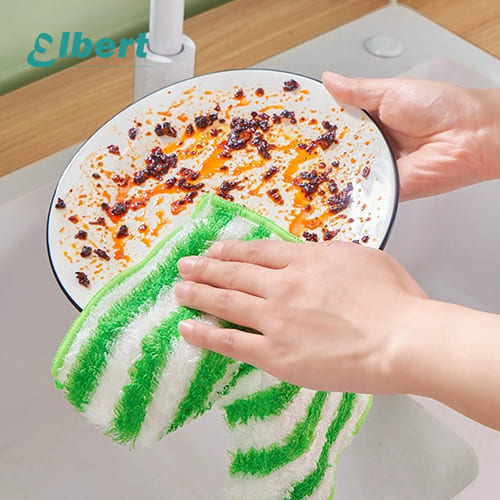
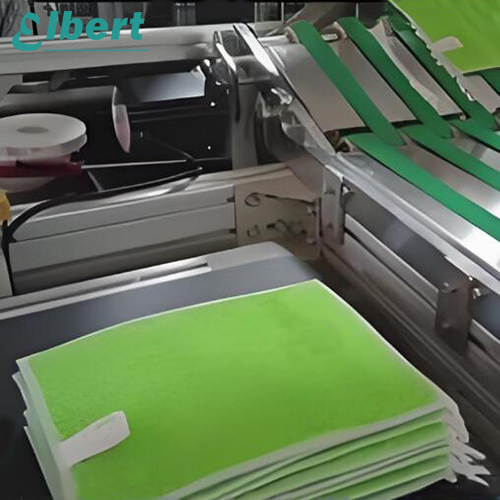
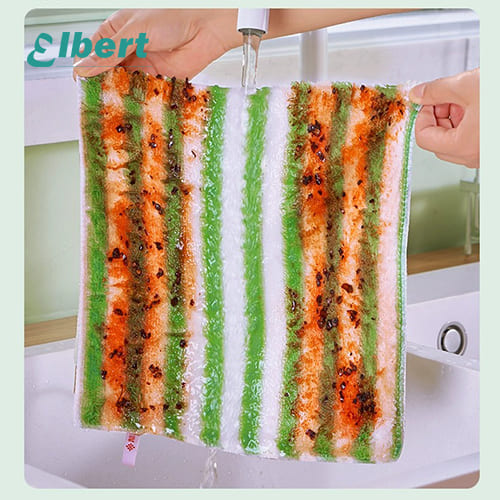
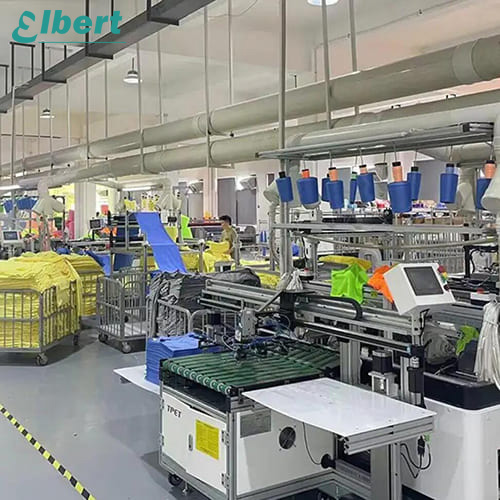
Overview of Bamboo Towel Manufacturing:
Bamboo towels are produced through a multi-step manufacturing process designed to turn raw bamboo fibers into strong, usable nonwoven fabrics. The key stages include fiber preparation, web formation, needle-punching, and post-processing:
-
Fiber Preparation: Bamboo stalks are converted into fibers either by mechanical or chemical means. In the mechanical method, bamboo is crushed and treated with enzymes to extract natural fibers (often called bamboo linen), an eco-friendly but labor-intensive process. More commonly, a chemical process is used to break down bamboo into cellulose (viscose rayon), which is then regenerated into fiber. The resulting bamboo fibers are short staples (similar to cotton fluff) that are cleaned, combed, and aligned. Manufacturers may blend bamboo fiber with a small percentage of other fibers (e.g. polyester or cotton) to enhance strength or processing efficiency, though 100% bamboo fiber can also be used for maximum biodegradability. This preparation stage ensures the fibers are ready to be formed into a fabric.
-
Web Formation: Prepared bamboo fibers are then formed into a loose web or batt. This is typically done using carding machines that comb the fibers into a thin, evenly distributed sheet. The carded web can be layered (cross-lapped) to build up the desired weight and thickness of the towel. The fibers in the web can be oriented randomly or in a specific direction depending on the performance needed. The goal at this stage is to create a uniform mat of fibers. In some modern processes, air-laid techniques may also be used, especially if blending bamboo pulp with other cellulose fibers. The output of web formation is a fragile fiber sheet that holds its shape just enough to be carried into the next stage.
-
Needle-Punching (Web Bonding): The weak fiber web is strengthened by mechanically entangling the fibers using a needle-punching machine. In this process, thousands of barbed needles repeatedly punch through the fiber web, grabbing and tangling fibers as they move up and down. This entanglement creates a cohesive nonwoven fabric without the need for any chemical binders. Needle-punching consolidates the web into a durable cloth by interlocking fibers vertically through the thickness of the material. The density and pattern of needle punches can be adjusted to control the fabric’s strength, thickness, and flexibility. The result after needle-punching is a rough, unfinished bamboo fiber fabric (sometimes called a bamboo felt) that has sufficient strength to be handled for further processing. This stage is crucial for achieving the high strength that bamboo towels are known for.
-
Post-Processing: After needle-punching, various finishing steps are applied to improve the fabric’s usability and appearance. The material may be trimmed or cut to size and subjected to heat-setting or calendaring (pressing between heated rollers) to smooth and stabilize it. If a blend of fibers was used (for example, a small amount of thermoplastic fiber), a light heat treatment can thermally bond those fibers, further increasing strength. The fabric can also be washed to remove any dust and to preshrink it. Additional treatments may be applied depending on the end-use – for instance, softening agents to make the towel feel softer, or chemical finishes to impart flame retardancy or water repellency for specialized applications. Dyeing or printing can be done at this stage if custom colors or patterns are desired. Finally, the finished bamboo towel material is rolled up or converted into the desired product form (such as wipes, sheets, or pre-cut towels) and packaged. Quality control tests (checking dimensions, weight, strength, absorption, etc.) are typically performed before the product is shipped. Post-processing ensures the bamboo towel meets the required specifications and is safe and pleasant to use.
Key Features of Bamboo Towels:
Bamboo fiber towels offer a range of notable features that make them attractive for industrial and commercial use:
-
High Strength: Bamboo-derived fibers have excellent tensile strength, which translates into durable fabrics. A single bamboo fiber can have a tensile strength on the order of 1.4–1.7 GPa, rivalling the strength of some synthetic fibers. The needle-punch manufacturing further boosts strength by densely entangling the fibers, yielding a towel that can withstand rigorous use without tearing. This high strength and toughness means bamboo towels hold up well in demanding applications (they resist punctures and abrasion better than many paper-based or polymer-based wipes of similar weight).
-
Breathability and Absorbency: Bamboo fiber is naturally breathable and has a high moisture absorbency. Nonwoven bamboo fabric can soak up water or spills readily, making it effective for wiping and cleaning. The structure of bamboo cellulose fibers allows air to pass through, so the material dries relatively quickly and resists trapping moisture. This breathability is a benefit in applications like filters or hygiene products where airflow is important. Bamboo-based fabrics also tend to feel cool and well-ventilated. Studies classify bamboo fabrics as having excellent moisture absorption and breathability. These properties help bamboo towels dry faster after use and prevent mildew, keeping them fresher in between uses.
-
Customizability: Bamboo towels can be customized in terms of thickness, size, and composition to suit different needs. Manufacturers can alter the basis weight (grams per square meter) of the needle-punched web, producing anything from thin, flexible sheets to thick, cushioned mats. The fiber blend is also customizable – while pure bamboo fiber is common for eco-friendly products, bamboo can be combined with cotton for extra softness, polyester for higher tear strength, or other natural fibers (like kenaf or jute) for specific performance traits. The material can be easily cut, sewn, or laminated with other layers if needed, allowing OEM partners to incorporate bamboo nonwoven into various product formats. Additionally, bamboo towels can be dyed or printed with logos and can be treated with coatings (e.g. an antimicrobial finish or fire retardant) during post-processing. This flexibility means clients can request a tailored bamboo towel product that meets precise specifications, from automotive insulation felts to branded reusable cleaning wipes.
-
Eco-Friendliness: Bamboo towels are an environmentally friendly alternative to synthetic textiles. Bamboo is a fast-growing, renewable resource that can be harvested sustainably. It typically requires far less water and no pesticides to cultivate compared to cotton. (For example, producing a bamboo-based fabric may use only a fraction of the water needed for an equivalent cotton fabric.) The production of nonwoven bamboo towels generally avoids harsh chemicals – mechanical fiber extraction and needle-punch bonding do not rely on toxic adhesives or solvents. Most importantly, bamboo towels are biodegradable and compostable when made of 100% bamboo or other natural fibers. They can decompose naturally at end-of-life, unlike polyester or polypropylene materials that persist as waste. This reduces landfill load and pollution. Using bamboo-based products can help companies meet sustainability goals and reduce their environmental footprint. Even during use, bamboo fibers have benefits: they contain a natural antimicrobial agent called bamboo kun that helps resist bacterial growth and odors, keeping the towels hygienic over repeated uses. Overall, the life-cycle environmental impact of bamboo towels is significantly lower than that of conventional microfiber or plastic-based towels, especially if the bamboo is processed in an eco-conscious way.
-
Cost Efficiency: Bamboo towels can offer cost advantages in the long term. The raw bamboo material itself is plentiful and grows rapidly (some species grow several feet per day), yielding a high volume of fiber per acre without the need for replanting after each harvest. As demand for sustainable textiles rises, economies of scale are improving for bamboo fiber processing, gradually bringing costs down. For businesses, using bamboo towels can also be cost-efficient because of their durability – they are sturdy enough to be reused many times, reducing the frequency of replacement compared to cheaper paper or thin synthetic wipes. Additionally, bamboo towels being biodegradable can save on disposal costs in industries where waste management is a concern (for instance, they can be composted instead of sent as hazardous waste if not contaminated with heavy chemicals). While the current unit price of a bamboo towel might be slightly higher than a mass-produced microfiber cloth, the overall value is competitive when factoring in sustainability and reusability. Clients often find that the performance and brand image benefits outweigh the marginal cost difference. Moreover, as manufacturing technology advances, bamboo towel production is becoming more efficient, further improving cost-effectiveness.
Applications Across Multiple Sectors:
Thanks to their strength, versatility, and eco-friendly nature, bamboo fiber towels (nonwoven mats and fabrics) are finding applications in a wide array of industries. Some notable sectors and uses include:
-
Filtration: Bamboo nonwoven material can serve as filter media in both air and liquid filtration systems. The fine yet strong fibers create a porous mat that can trap dust, particulate matter, or impurities while allowing airflow or water flow. For example, bamboo fiber felts can be used in HVAC air filters or industrial dust collectors as a biodegradable alternative to synthetic filter fabrics. In water filtration, bamboo mats can act as pre-filters or support layers in composite filter cartridges. The breathability and moisture resilience of bamboo towels make them suitable for filters, and their natural antibacterial properties are a bonus in water or medical filtration to inhibit microbial growth on the filter medium. Needle-punched nonwovens like bamboo are already used in filtration and battery separators, indicating the viability of bamboo in these technical applications.
-
Geotextiles: In civil engineering and environmental projects, bamboo fiber mats function as geotextiles for soil stabilization, erosion control, and landscaping. They can be laid on soil to prevent erosion on slopes, riverbanks, or construction sites, much like jute or coir erosion blankets. Bamboo geotextiles have the advantage of being strong and biodegradable, gradually decomposing and adding organic matter to soil after serving their purpose. Research has shown that woven bamboo geotextiles can effectively reduce soil erosion on steep slopes, performing on par with or better than coir mats. Nonwoven bamboo felts can also be used under roads or pavers to separate soil layers and improve ground stability (replacing synthetic polypropylene geotextiles). Since bamboo fibers naturally resist rot for a period, they can stabilize soil during critical periods and then break down without leaving pollutants. This makes them attractive in green infrastructure and landscape architecture projects aimed at sustainability.
-
Automotive Interiors: The automotive industry is exploring bamboo fiber nonwovens for interior components and insulation. Natural fiber felts are used in car door panels, headliners, trunk liners, and floor underlays for sound insulation and weight reduction. Bamboo, along with fibers like flax and kenaf, is being considered to replace a portion of synthetic fibers in these composites. A needle-punched bamboo mat can serve as an acoustic insulation layer, dampening engine and road noise inside the vehicle cabin. It can also be molded (when blended with a thermoplastic binder or resin) into rigid panels for door or trunk linings. The appeal is that bamboo-based materials are lighter than traditional fiberglass or plastic parts and are recyclable or biodegradable. They also often have a lower embodied energy. Car manufacturers value that natural fibers like bamboo can offset the environmental impact of synthetic materials while meeting performance needs. Bamboo interiors can lend a marketing edge as well, positioning a vehicle as more eco-conscious. Additionally, bamboo charcoal nonwovens have been used in car air purification filters and seat cushion pads due to their odor-absorbing qualities.
-
Household Cleaning: Bamboo towels are increasingly used as cleaning wipes and kitchen towels. In the household sector, they appear as reusable cleaning cloths that can wipe surfaces, absorb spills, and dust furniture. The high absorbency of bamboo towels makes them excellent for kitchen use – for instance, wiping counters or drying dishes. Unlike disposable paper towels, bamboo towels can be rinsed and reused many times, offering consumers an eco-friendly cleaning option. They are also sold as bamboo paper towel replacements: one perforated roll of bamboo fiber sheets that can be washed and reused, replacing dozens of single-use paper towel rolls. Their natural antibacterial property helps keep kitchen cloths more sanitary, and they tend not to develop odors as quickly as cotton rags might. Bamboo cleaning wipes are tough on dirt but gentle on surfaces – they won’t scratch glass or stainless steel, in contrast to some microfiber cloths that can cause micro-scratches over time. This makes them suitable for cleaning windows, eyeglasses, or electronics screens. In sum, for households and commercial cleaning services, bamboo towels provide a durable, lint-free, and green cleaning solution.
-
Industrial Wipes: In industrial settings, heavy-duty wipes made from bamboo nonwoven fabric are used for tasks like wiping machinery, absorbing oil spills, or polishing equipment. These wipes benefit from bamboo’s strength (they don’t tear easily even when wet) and absorbency (useful for soaking up oils or solvents). Factories and workshops can use bamboo shop towels to replace synthetic shop rags. Because they are biodegradable, contaminated bamboo wipes used with grease or chemicals can be disposed of more responsibly (some can even be incinerated for energy recovery without releasing harmful plastic residues). Bamboo industrial towels can be designed to be low-lint, which is important in environments like automotive paint shops or electronic assembly where stray fibers must be minimized. They can also be made in large formats (e.g., wipes the size of a bed sheet) for big cleaning jobs or as drop cloths. The industrial use of bamboo towels demonstrates their multifunctionality and durability in harsh conditions, from construction sites to manufacturing floors.
-
Insulation: Both thermal and acoustic insulation materials can be made from bamboo fiber felts. In building construction, bamboo nonwovens can act as natural fiber insulation batts in walls or attics, similar to how mineral wool or fiberglass is used. The advantage is that bamboo fiber is a safer, non-itchy material that does not off-gas and is biodegradable. It can provide decent thermal insulation due to the air pockets trapped in the fiber network. Additionally, bamboo fiber’s moisture-regulating ability can help prevent condensation issues in insulation. For sound insulation, layers of needle-punched bamboo mats can line walls, ceilings, or machinery enclosures to absorb noise. The random fiber structure dissipates sound waves effectively. Bamboo-based acoustic panels could be used in recording studios or offices as an eco-friendly alternative to polyurethane foam panels. In the automotive and aerospace industries, as mentioned, these felts serve as lightweight insulation for noise and heat. The use of bamboo in insulation is part of a trend of adopting natural fibers (like bamboo, flax, or hemp) to improve sustainability in construction materials while maintaining performance.
-
Packaging Material: Bamboo fiber has even made its way into packaging applications. Rigid packaging foams and inserts can be replaced with bamboo fiber mats or molded pulp, which cushion products during shipping. For example, Lenovo introduced packaging cushions made from 100% bamboo fiber to protect electronics, reducing reliance on plastic foams. The bamboo packaging inserts provided a lightweight yet robust support for products and allowed a 30% reduction in box weight. Because bamboo fibers are 100% renewable and compostable, this kind of packaging is attractive for companies looking to cut down on plastic waste. Bamboo nonwoven sheets can also be laminated to paper or starch films to create fully biodegradable packaging wraps and pouches. In addition, bamboo’s shock-absorbing capacity (when formed into a felt) makes it useful as a liner in crates or as a material for protective sleeves for delicate instruments. We also see bamboo fiber being used in food packaging – for instance, disposable plates, trays, and containers made by pressing bamboo fiber pulp, which are sturdier than paper products. Overall, packaging is a growth area for bamboo fiber usage, capitalizing on its renewable nature and protective qualities.
Other Potential Uses:
Beyond the major sectors above, bamboo towels have potential in several other areas:
-
Agricultural Covers: Bamboo nonwoven fabrics can function as crop covers, frost blankets, or weed-suppressing mats in agriculture. Placing a lightweight bamboo fiber sheet over crops can protect them from insects or cold snaps while still allowing light and water through (thanks to the material’s breathability). Since the bamboo textile is biodegradable, farmers can till it into the soil after the growing season, improving soil organic content. Similarly, as a weed barrier, a bamboo felt laid on garden beds could block weeds and then decompose after a couple of years, avoiding the labor of removal that synthetic weed mats require. This concept is analogous to using straw or jute mats in agriculture, with bamboo providing potentially higher strength and uniformity. Another agricultural use is in nursery grow bags – nonwoven pots made of bamboo fiber that can be planted directly into the ground, where the bag breaks down naturally. This reduces transplant shock and plastic waste from seedling pots. Although these uses are still emerging, they demonstrate bamboo towels’ adaptability in the agricultural field, aligning with the push for sustainable farming practices.
-
Medical and Hygiene Supplies: Bamboo fiber is gaining attention in medical textiles. The natural antibacterial properties of bamboo-derived fabric make it appealing for items like hospital wipes, patient gowns, and bed linens, where reducing bacterial spread is vital. Bamboo nonwoven swabs or gauze could be used for wound dressings that are gentle on skin and biodegradable after use. In fact, the healthcare sector is exploring bamboo for disposable products such as surgical masks, caps, and shoe covers – usually made from polypropylene – to create more eco-friendly alternatives. Bamboo’s breathability and softness are advantageous for these applications, providing comfort to the wearer. There are research efforts to enhance bamboo medical textiles with extra functionalities: for example, one study created multifunctional medical nonwoven fabrics from bamboo fiber with added superhydrophobic and flame-retardant coatings, achieving high water repellency and 99% antibacterial activity against common pathogens. This indicates that bamboo-based medical supplies could be engineered to meet strict performance requirements while remaining sustainable. Even personal care and hygiene products like diaper liners, sanitary napkin covers, or facial wipes are being made with bamboo fiber due to its softness and hypoallergenic nature. In summary, bamboo towels and nonwovens hold promise in medical and sanitary uses where single-use disposables have traditionally created significant plastic waste.
Comparison with Microfiber Towels:
Microfiber towels (made of synthetic fibers like polyester/polyamide) are a common alternative to bamboo towels in many applications. Below is a comparison of the two across key criteria:
-
Performance (Cleaning & Absorbency): Bamboo towels are highly absorbent and can hold a great deal of liquid relative to their weight, making them excellent for wiping spills or drying. They are effective at general cleaning and polishing, and their slightly textured fiber structure helps pick up dust and dirt. However, on heavy grease or oil, bamboo cloths may be slightly less effective than microfiber due to the fiber surface characteristics. Microfiber towels, by contrast, excel at gripping and lifting oily dirt and microscopic particles. The ultrafine synthetic fibers and their split edges create a larger surface area that can attract and hold grease and dust, often without needing much chemical cleaner. This makes microfiber very popular for tough cleaning jobs and automotive detailing. In absorbency, good microfiber towels can also hold many times their weight in water. In practice, both materials absorb well, but microfiber’s edge in tackling grease and very fine particles makes it slightly more performant for certain cleaning tasks. Bamboo towels perform robustly for most uses, and importantly, they maintain performance over repeated use (they don’t lose absorbency quickly).
-
Eco-Friendliness: Bamboo towels are the clear winner in sustainability. They are made from a renewable plant resource and are biodegradable at end-of-life. Production of bamboo fiber can be done with low environmental impact if mechanical or closed-loop processes are used. Additionally, no microplastics are shed from bamboo towels during washing or use – any fiber that wears off is natural cellulose that will break down harmlessly. Microfiber towels, on the other hand, are made from petroleum-based plastics. Every time a microfiber cloth is washed, it can release tiny synthetic fibers (microplastics) into wastewater. These microplastics are not biodegradable and have been found to pollute rivers and oceans. Moreover, microfiber manufacturing relies on non-renewable resources and can be energy-intensive. While microfiber towels are reusable (reducing paper waste), their end-of-life typically leads to landfill or incineration since the plastic fibers cannot easily be recycled. In short, bamboo towels offer a much smaller environmental footprint – from production to disposal – compared to microfiber, which carries hidden long-term costs to the environment.
-
Durability: Microfiber towels are very durable in the sense that the synthetic fibers themselves are strong and don’t biologically degrade. A high-quality microfiber cloth can endure hundreds of wash cycles with minimal loss in performance, and the material doesn’t easily tear. However, durability has a double side: the fibers are so persistent that if they enter the environment, they last for decades (or longer) as pollution. Bamboo towels are also quite durable for repeated use, especially if made with a dense needle-punched structure. They will typically survive dozens of washes and heavy-duty usage. Bamboo fibers have good tensile strength and the towels maintain integrity well. That said, because they are natural, they will eventually wear out a bit faster than a polyester microfiber might – for instance, after a great number of wash cycles, a bamboo towel might start to fray or thin out sooner. In applications like industrial uses or where the towel may be exposed to harsh chemicals, a polyester microfiber might resist chemical attack slightly better than a natural fiber. Even so, many users find bamboo towels sufficiently robust for their needs, and appreciate that when a bamboo towel does wear out, it won’t harm the environment. In terms of long-term durability, microfiber has the edge in lifespan, but bamboo towels are durable enough for extensive reuse and have the advantage of graceful degradation (they simply biodegrade instead of becoming persistent waste).
-
Softness & Surface Safety: Bamboo towels have a naturally soft feel (especially if the fibers are processed via the viscose method, they can be very silky). When used on surfaces, bamboo fiber cloths are gentle and non-abrasive. They do not contain the microscopic abrasive particles that some microfiber weaves can have, so they are safe to use on delicate surfaces like glass, polished stone, or automotive paint without risk of scratching. This makes bamboo towels great for tasks like wiping eyeglass lenses or car exteriors. The texture of a bamboo towel is often described as smooth yet slightly fibrous (comparable to a fine cotton or linen feel). Microfiber towels are also soft to the touch, but their synthetic fiber structure can cause issues on sensitive surfaces. The tiny fibers in a microfiber cloth can act like mild sandpaper over long-term use, leading to microscratches on high-gloss surfaces (like camera lenses, eyeglasses, or clear coat finishes) if not used carefully. Some microfiber towels have a very plush finish which is gentle, but others (especially cheaper ones) can feel a bit grabby against the skin or drag on dry surfaces due to their high friction. In terms of user comfort, many people find bamboo towels pleasant and non-irritating (bamboo fabric is noted to be good for sensitive skin). Both types can be made quite soft, but bamboo’s natural silkiness gives it an edge for comfort and safety on delicate jobs.
-
Cost: Microfiber towels are generally less expensive to produce and purchase. Made in huge volumes from cheap polymers, a standard microfiber cleaning cloth is very low-cost per unit. For bulk industrial supply, microfiber can often be the cheapest choice upfront. Bamboo towels tend to be a bit higher in price, mainly due to the cost of processing bamboo fibers and presently smaller production scale. The manufacturing processes for bamboo (especially if using eco-friendly methods) are still more costly than melting and extruding plastic fibers. However, the cost gap has been narrowing as technology improves and demand grows. It’s also worth considering the hidden costs and value-add: bamboo towels can enhance a company’s sustainability profile, potentially providing marketing value or meeting regulatory requirements (justifying a higher price). And if a bamboo towel can be reused and lasts a long time, the cost per use can become very low. In specialized uses (like medical or high-tech manufacturing), the cost difference may be negligible compared to the benefits. In summary, microfiber wins on raw price and wide availability, but bamboo towels offer competitive lifecycle value and align with the increasing emphasis on sustainability in procurement decisions.
-
Customizability: Both bamboo and microfiber towels are quite customizable, but there are some differences. Microfiber towels can be manufactured in various weaves (terry, waffle, suede, etc.), different fiber blends (70/30 polyester-polyamide, 80/20, etc.), and a rainbow of colors through synthetic dyes. They can also be made in different pile heights (some are flat woven for glass cleaning, others are thick and fluffy for drying). The synthetic nature means they can even incorporate patterns or embossing (for example, some microfiber cleaning pads have scrubbing strips or printed designs). Bamboo towels (specifically the nonwoven type we discuss) can be customized mainly by adjusting the manufacturing parameters: fiber blend, weight, thickness, and post-treatment. They can be made thinner for lens cloths or thick and felt-like for padding applications. Blending bamboo with cotton or other fibers can alter the texture and strength. Bamboo fibers take natural dyes fairly well, though the color range might be slightly more limited than neon-colored synthetics. Printing on bamboo nonwoven is possible, for instance to add a company logo on a shop towel. One area where bamboo is less versatile is at extremely fine fiber diameters – microfiber’s advantage is the ultra-fine fiber structure (often 10 microns or less). Bamboo fibers, even viscose, are usually not as fine as the finest microfibers, so you can’t replicate the exact same texture as a suede-style microfiber lens cloth, for example. Nonetheless, bamboo towels cover most needs and can be tailor-made by varying the processing (e.g., needling intensity for texture, or adding a scrim layer for extra strength). For OEM partners, bamboo towels can be supplied in rolls or sheets to be further converted into finished products as required, offering flexibility in integration.
(See comparison summary in Table 1 below.)
Table 1: Bamboo Towels vs. Microfiber Towels – Comparison of Key Attributes
Aspect | Bamboo Towels | Microfiber Towels |
---|---|---|
Performance |
Excellent absorbency for water; effective general cleaning. Slightly less adept at lifting heavy grease without cleaner. Provides good dust pickup and polishing. |
Extremely high absorbency and particle pick-up, including oils. Cleans grease and fine dust often without chemicals. Ideal for tough grime. |
Eco-Friendliness |
Made from renewable bamboo; biodegradable and compostable. No microplastic shedding or pollution. Low-impact cultivation (uses minimal water/pesticides). |
Made from synthetic polymers (polyester/polyamide). Not biodegradable; releases microplastic fibers when washed. Relies on petrochemicals. |
Durability | Strong and durable for many reuse cycles. Will eventually biodegrade (a positive for disposal). Typically lasts through dozens of washes. | Very durable and long-lasting through hundreds of washes. Resistant to biological decay (plastic fibers). Can endure heavy-duty use without tearing. |
Softness & Surface Safety |
Soft and smooth feel; safe on sensitive surfaces (won’t scratch). Good for skin contact (hypoallergenic). Texture comparable to cotton/linen. |
Soft to touch, but can cause micro-scratches on paint or glass over time if used improperly. Some weaves are extremely plush; others can feel tacky on skin. |
Cost | Moderate cost – slightly higher per unit due to fiber processing. Costs dropping as scale increases. Offers value through reusability and sustainability benefits. | Low cost – inexpensive mass production. Widely available and affordable in bulk. However, no environmental value-add (disposal and pollution costs externalized). |
Customizability | Custom weights/thickness; can blend with other fibers; can be cut or sized to spec. Dyeable in natural colors; printable. Fiber is somewhat limited to certain fineness. | Highly customizable in fiber blend and fabric style (weaves, pile heights). Easy to dye any color. Can be engineered for different textures (silky, fluffy, etc.). Very fine fiber options available. |
Advantages and Limitations of Bamboo Towels:
In summary, bamboo towels present a compelling mix of benefits, but also a few limitations that are important to consider in a business context.
Key Advantages:
-
Multifunctionality: Bamboo fiber towels are extremely versatile, as demonstrated by their use in everything from filtration units to cosmetic wipes. A single material can fulfill multiple roles – absorbing liquids, reinforcing composites, filtering air, protecting soil – which can simplify supply chains. For OEMs, this means a bamboo nonwoven roll stock might be adaptable to various product lines (one fabric could be cut into both cleaning cloths and packaging liners, for example). This multi-use nature is a strength; companies can innovate new applications around the base material.
-
Durability and Strength: As highlighted, bamboo towels are robust. They maintain integrity under stress, whether that’s an industrial wiping task or serving as an automotive insulation pad. Unlike paper-based alternatives that tear easily or have low wet strength, bamboo fiber fabric stays strong when wet. It also handles stretching and twisting without disintegrating. One practical advantage of this durability is reduced wastage – end users can rinse and reuse a bamboo wipe multiple times, or count on a bamboo geotextile to last through a rainy season in the field. Additionally, bamboo fibers can be engineered into composites for even greater strength (combining bamboo nonwoven with resins or other fibers to create panels or molded parts), showcasing their material toughness.
-
Eco-Performance: Bamboo towels offer environmental performance that aligns with green business goals. They are made from a low-impact raw material and are themselves low-impact at disposal. This gives them an edge in an era of increasing environmental regulations and consumer preference for sustainable products. For instance, a company that switches from polyester shop rags to biodegradable bamboo towels can immediately reduce plastic waste generation. If a spill cleanup uses bamboo pads, those used pads can potentially be composted (if they aren’t soaked in hazardous chemicals) rather than landfilled. Bamboo’s fast growth and carbon sequestration during cultivation are additional eco-benefits that, while not directly a feature of the towel, contribute to a positive story for marketing and corporate responsibility reports. Simply put, using bamboo textiles can help companies reduce their carbon and waste footprint and meet targets for sustainable sourcing.
-
Natural Antibacterial Properties: Bamboo fiber inherently contains antimicrobial bio-agents (like “bamboo kun”) that give it resistance to bacterial growth and odors. While this doesn’t make bamboo towels sterile, it means they are less prone to developing bad smells or harboring lots of bacteria compared to cotton or sponges. This is an advantage in hygiene-critical uses or when towels are reused over time. Some studies indicate that bacteria find it harder to proliferate on bamboo-based fabrics. In practical terms, a cleaning cloth made of bamboo might stay fresh longer and require less frequent washing than a synthetic cloth, which can slime up with bacterial film if left damp. This contributes to both user convenience and potentially better sanitary conditions.
-
Thermal Regulation: Bamboo fiber has insulative properties and a degree of heat resistance. Bamboo towels can act as a mild insulator – for example, they can be used as a heat shield pad on a workbench when handling moderately hot items, where a plastic towel might melt. Also, as a lining in apparel or bedding, bamboo nonwovens help keep a comfortable temperature (they’re breathable and wick moisture, cooling when hot and providing insulation when cool). This is why bamboo blankets and batting are emerging in the textile market. For OEMs making products like cooler bags or thermal packaging, a layer of bamboo fiber padding can enhance performance.
Key Limitations:
-
Rougher Texture (Compared to Wovens or Microfiber): While bamboo fiber itself can be soft, a needle-punched bamboo towel has a different feel than a traditional woven cotton or a plush microfiber cloth. The texture is typically flat and felt-like; for some applications this is perfectly fine (even beneficial for scrubbing ability), but for others it might be perceived as less gentle or less “luxurious” to the touch. For instance, as a bath towel, 100% bamboo needle-punch felt would feel quite different from a soft terry cotton towel – it would be thinner and less fluffy. In cleaning uses, the slightly rough texture is usually not an issue and can help scour dirt, but if absolute softness is needed (such as wiping a newborn’s skin), bamboo nonwovens might need a surface finishing or blending with cotton to improve feel. Essentially, bamboo towels aren’t plush unless additional processing is done. This is a trade-off: the product sacrifices a bit of surface smoothness for the sake of strength and simplicity of manufacturing. However, note that some bamboo towels on the market are actually a bamboo-rayon textile looped like terry cloth, which are very soft – those are made by a different process (spun yarn weaving) and not the focus here. For the nonwoven bamboo towels, a slightly coarse handfeel is a minor limitation to be mindful of.
-
Higher Production Cost (Currently): Producing bamboo fiber and nonwovens tends to cost more than producing common synthetic microfiber. The specialized processing (especially if using eco-friendly methods like the mechanical or lyocell process) and smaller scale of bamboo textile manufacturing contribute to a higher price point. As noted in market analyses, the cost of processing bamboo fiber is still relatively high compared to conventional materials. This can make bamboo towels more expensive for now, which could be a barrier for some cost-sensitive bulk buyers. Additionally, if comparing to commodity products like polypropylene wipes or polyester felt, bamboo’s price per kilogram is higher. Over time, as technology advances and production ramps up, these costs are expected to come down. But in the present market, companies considering bamboo towels need to justify the premium through the benefits (sustainability, performance, branding). In some cases, blending bamboo with cheaper fibers can reduce cost, but that might compromise the eco-friendly profile. Thus, cost is a limitation mainly in the context of large-scale, budget-focused procurement. It’s worth noting that cost evaluations should include end-of-life savings or compliance benefits – for example, using biodegradable towels might save waste disposal fees or help avoid regulatory fines, partially offsetting the initial higher price.
-
Moisture Sensitivity and Drying Time: Bamboo fiber, being very absorbent, will hold moisture. If bamboo towels are left wet or stored in humid conditions, they can take longer to dry out than a quick-drying synthetic cloth. This isn’t a severe limitation, but it means that in very damp environments, a bamboo towel should be properly hung to dry to avoid any moldy smell (as with any cellulose material). Microfiber, by contrast, is hydrophobic and can air-dry faster. So for scenarios like an expedition backpacker’s towel that must dry ultra-fast, pure bamboo might be less ideal (though blends and design can mitigate this). For most industrial uses, drying time is not a big issue, but it’s a consideration for product design.
-
Chemical Processing Concerns: If the bamboo fiber is produced via the viscose rayon process, there are environmental considerations (use of solvents like sodium hydroxide and carbon disulfide). Some critics note that bamboo rayon, in spite of coming from bamboo, can involve toxic chemicals in production. However, many manufacturers now use closed-loop systems to recapture and reuse chemicals (as in bamboo lyocell production) to address this. This is more of an industry challenge than a limitation of the towel’s performance, but it’s worth mentioning for transparency. Truly “green” bamboo towels should be made with the newer eco-friendly processes. OEM partners sometimes ask about this, so understanding the distinction can be important. In essence, the limitation is that not all bamboo textiles are equally eco-friendly in processing, and choosing a reputable source is important to ensure the sustainability claims hold true.
-
Availability and Supply Chain: Bamboo textile supply is growing but is not as ubiquitous as cotton or polyester. Large-volume orders might require scheduling with producers well in advance. The supply chain for quality bamboo fiber is still maturing – most bamboo fiber comes from Asia (notably China, where bamboo is plentiful and the industry is established). This could mean longer lead times for Western companies and potential supply bottlenecks. However, this situation is rapidly improving as global demand increases and more producers enter the market. It’s a consideration that currently, sourcing bamboo towels might not be as instantaneous as ordering standard synthetic fabrics off the shelf.
Despite these limitations, many businesses find that the advantages of bamboo towels far outweigh the drawbacks, especially as technology and scale improve. The rougher texture can be addressed in many cases (either it’s not critical for the use, or it can be improved), and the cost is increasingly justified by environmental accountability and consumer preference trends.
Market Demand and Development Trends:
The market for bamboo fiber products, including towels and nonwoven fabrics, is experiencing strong growth driven by sustainability trends and technological advancements.
Recent market analyses show a clear rise in demand for bamboo-based textiles worldwide. In 2025, the global bamboo fiber market (which encompasses apparel, home textiles, hygiene products, etc.) was valued around $1.5 billion, and it is projected to grow to about $2.8 billion by 2033, which represents a healthy CAGR of roughly 8%. This growth outpaces many traditional textile segments, indicating a robust interest in bamboo materials. Several factors contribute to this trend:
-
Increased Demand for Eco-Materials: Governments, corporations, and consumers are all pushing for greener materials. Bamboo’s renewability and biodegradability make it a prime candidate to replace plastics and cotton in many uses. For example, there is rising adoption of bamboo in single-use products (wipes, packaging, medical disposables) to reduce plastic waste. Companies are also looking to improve their ESG (Environmental, Social, and Governance) scores by incorporating sustainable materials like bamboo. This broad sustainability movement forms the backbone of market expansion for bamboo towels.
-
Performance and Functional Upgrades: Early bamboo fabrics were sometimes seen as niche or inferior in performance to synthetics, but that is changing fast. Ongoing R&D is yielding bamboo textiles with enhanced functionalities. A clear trend is the development of multifunctional bamboo nonwovens – materials that offer not just basic utility but added features like antimicrobial action, UV resistance, or fire retardancy. For instance, researchers have created bamboo-based medical nonwovens that are superhydrophobic and flame-retardant without sacrificing biodegradability. We also see new bamboo composite materials (blends of bamboo fiber with biodegradable polymers) that improve strength and water resistance, opening up applications in outdoor textiles and even in structural components. This innovation wave means bamboo towels and fabrics are steadily closing any performance gap with synthetic products, and even offering new benefits synthetic products lack (such as inherent biodegradability combined with advanced coatings). As a result, more industries find bamboo materials to be not just an eco-friendly choice, but also a technically competitive one.
-
Smart Manufacturing and Process Automation: The textile industry, including nonwovens, is undergoing a transformation with Industry 4.0 principles. “Smart manufacturing” refers to increased automation, digital monitoring, and precision in production. In the context of bamboo towels, smart manufacturing can help reduce costs and improve quality consistency. For example, modern fiber opening and carding systems can use optical sensors to ensure the blend is consistent, and needle-punch machines can be equipped with computer control to optimize needle density and pattern for the best strength with minimal fiber use. Innovations like DiloGroup’s 3D-Lofter technology allow fiber deposition in specific zones of a nonwoven web to reinforce weak points and save raw material – such techniques could be applied when making bamboo felts to use fibers more efficiently (up to 30% fiber savings reported). Additionally, automation in handling and packaging means bamboo towel products can be made with less labor, offsetting higher material costs. Smart manufacturing also encompasses sustainable production improvements: recycling water used in processing, using renewable energy in factories, and integrating quality control sensors to minimize defects and waste. All of these developments contribute to making bamboo towel production more scalable and cost-effective, which is a notable trend as we head towards 2030. The outcome will be higher output and possibly lower prices, further fueling adoption.
-
Market Diversification and Geographic Spread: Initially, bamboo textiles found popularity in niches like organic baby products and luxury bath linens. The current trend is diversification into many sectors (as we’ve outlined in applications). It’s not just one market segment growing – we see simultaneous uptick in automotive interest, in consumer home goods, in medical supplies, etc. Geographically, Asia-Pacific remains the largest producer and consumer of bamboo fiber (with China and India leading production). But North America and Europe are increasingly embracing bamboo materials, driven by both consumer demand and import of technology. There’s also interest in developing local bamboo industries in countries where bamboo grows (parts of Africa, South America), which could further expand the global supply base. So the trend is both an expanding market size and a more distributed production landscape, reducing reliance on any single region over time.
-
Regulatory Support: Another driver is the regulatory environment – many governments are setting targets for biodegradable materials and restricting single-use plastics. For instance, certain plastic wipes and bags are being banned or taxed. This directly benefits products like bamboo wipes and packaging, as businesses seek compliant alternatives. We can expect future regulations to continue favoring compostable, renewable materials, providing a tailwind for bamboo towel adoption in industries like food service, healthcare, and public facilities.
Global Bamboo Fiber Market projected growth from 2025 to 2033 (market size in USD billions, approximate). The upward trend reflects increasing demand for sustainable textile materials.
The chart above (Figure 1) illustrates the projected growth trajectory of the global bamboo fiber market. As shown, the market size is expected to nearly double over the 2025-2033 period. This growth encapsulates not only bamboo towels but all uses of bamboo fiber. Nevertheless, nonwoven applications like wipes and technical textiles are an important part of this expansion, especially as industries seek greener materials. Analysts note that continued innovation and economies of scale will be key to maintaining this growth; if the cost barriers lower and more success stories of bamboo integration emerge, the demand could accelerate even further.
In terms of future outlook, we anticipate bamboo towels becoming a standard option offered by suppliers in various industries, rather than a specialty item. The development of blended solutions is one trend – for example, mixing bamboo fiber with recycled polyester to create a product that is partially biodegradable yet meets very high strength requirements, or blending bamboo with cotton to appeal to both sustainability and luxury (softness) markets. Another expected trend is certification and standardization: as the market matures, clients will look for certifications (like FSC for bamboo sourcing, or ASTM standards for biodegradability) to ensure the bamboo products meet certain benchmarks. This is similar to how organic cotton or recycled PET fabrics are certified today. The ELBERT brand, by proactively focusing on bamboo towels, is positioning itself ahead of this curve, ready to meet the rising demand with proven expertise and supply chain readiness.
Finally, the concept of “smart” or “intelligent” textiles might also touch bamboo nonwovens. We might see bamboo towel materials integrated with sensors or conductive fibers for IoT applications (e.g., a smart cleaning cloth that can signal when it’s contaminated, or a bamboo fiber-based filter that changes color when saturated). While speculative, it’s worth noting that natural fibers are not excluded from the smart textiles revolution – they can be carriers for coatings or electronics just as synthetics can. If such technologies become viable, bamboo’s compatibility with them would add another dimension to its applicability.
Conclusion:
Bamboo towels offer a harmonious blend of performance, versatility, and sustainability. From their carefully engineered manufacturing process – starting with fiber extraction and ending with a finished, functional textile – to their wide range of applications across industries, bamboo fiber towels represent a forward-looking material solution for businesses. They bring high strength, breathability, and customizability, satisfying technical requirements in uses as diverse as automotive parts and kitchen wipes. At the same time, they address the urgent need for eco-friendly materials: being renewable, biodegradable, and generally having a smaller environmental footprint than conventional textiles. The comparison with microfiber towels highlights that while each material has its place, bamboo towels excel in eco-friendliness and hold their own in most performance aspects, making them an increasingly attractive choice especially where sustainability is a priority.
As with any material, bamboo towels have their limitations – a slightly different feel, and currently a somewhat higher cost – but ongoing developments in the industry are rapidly mitigating these factors. Market trends point to growing demand, which will likely spur further improvements in production efficiency and material properties. The commitment to sustainable development, coupled with innovations in manufacturing (like smart needling techniques and functional finishing), is paving the way for bamboo towels to become even more cost-effective and high-performing. Companies investing in or partnering on bamboo towel products today can gain an early-mover advantage, establishing themselves as leaders in quality and sustainability.
For ELBERT and its OEM partners, embracing bamboo towels aligns well with the values of innovation and environmental responsibility. By offering bamboo towel solutions, ELBERT can meet the needs of business clients who are seeking not just a product, but a story – a story of technological craftsmanship and sustainable choice. With the knowledge provided in this overview, B2B clients can confidently consider bamboo towels for their applications, armed with an understanding of how they are made, what features they offer, and how they compare to traditional options. The continued evolution of bamboo textiles promises exciting opportunities ahead, and ELBERT stands ready to deliver on those opportunities with expertise and reliability.
Elbert Zhao
Founder, ELBERT Wipes Solutions
📧[email protected] | 🌐 www.elbertwipes.com
8 production lines | 22 processing lines | OEKO-TEX certified | Walmart-approved supplier