High and Low Pile Microfiber
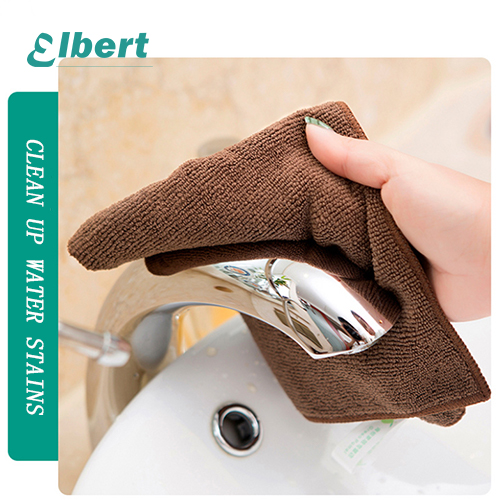
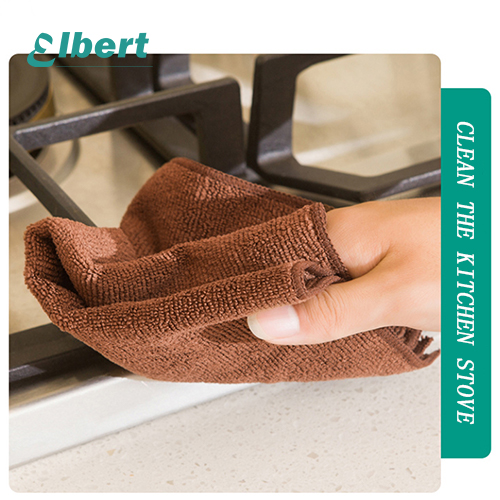
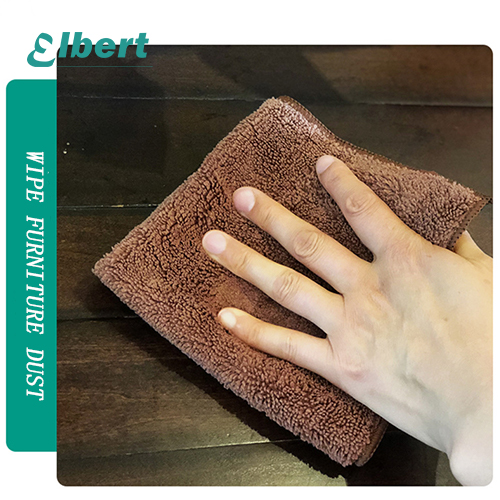
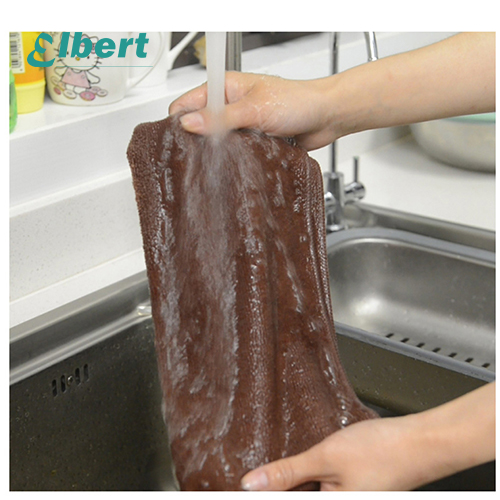
-
Introduction to High and Low Pile Microfiber
Microfiber is a synthetic fiber that is extremely fine – often thinner than a strand of silk. These ultra-fine fibers are typically made of polyester, polyamide (nylon), or a blend. They are woven or bonded into fabrics with unique softness and high performance. In microfiber textiles, the term “pile” refers to the length and density of the fiber loops or strands on the surface. A high pile microfiber has longer, fluffier fibers, giving the material a plush, thick feel (imagine a fuzzy towel or cloth). In contrast, a low pile microfiber has shorter, tighter fibers, resulting in a smoother, flatter surface (like a glass cleaning cloth). This difference in pile affects how the material behaves. For example, a high pile cloth can trap more dust and liquid in its fibers, while a low pile cloth makes more direct contact with a surface for wiping. One auto detailing expert neatly summarized the distinction: “High pile = more absorbent, carries dirt deeper into the cloth… great for removing waxes. Short pile = better streak-free finish, ideal for glass or final wipes.” In other words, high pile microfiber is excellent for soaking up liquids and gently lifting particles, whereas low pile is superb for polishing and leaving surfaces clear of streaks. This concept is important for buyers because choosing the right type of microfiber (high or low pile) will depend on the intended application – whether it’s a polishing towel, an upholstery fabric, a filter material, or something else.
Basic comparison of high pile and low pile microfiber characteristics. High pile microfiber has longer fibers creating a fluffy, plush texture, whereas low pile has short fibers for a smooth, firm touch. These differences influence absorbency and use-cases: high pile materials hold more dust and liquid, while low pile fabrics wipe clean with minimal lint, as reflected in the table above.
From a business perspective, understanding these differences helps in making informed decisions when sourcing materials. As the founder of a company specializing in nonwoven wipes and microfiber towels, I often educate our partners on selecting the appropriate pile type for their products. High pile microfiber might be preferable for applications needing cushioning and high absorbency (for instance, a deluxe cleaning towel or a filtration pad), whereas low pile microfiber works well for applications needing a flat, smooth finish (such as a lens wipe or a medical cloth). In the next sections, we will explore how microfiber materials are made, their key features, and how they are used across various industries.
-
Manufacturing Process: Fiber Preparation, Web Formation, Needle Punching, Post-Treatment
Microfiber fabrics can be produced through different methods. One common manufacturing method, especially for nonwoven microfiber textiles, is the needle-punching process. This process turns loose fibers into a coherent fabric without traditional weaving. It involves several stages:
-
Fiber Preparation: First, raw fibers are prepared for processing. In this step, the manufacturer chooses the fiber composition (for example, polyester microfibers, sometimes blended with other fibers for specific properties) and prepares them by opening bales, cleaning if necessary, and creating a uniform fiber supply. The fibers may be blended to combine different qualities (such as a mix of coarse and fine fibers, or adding a portion of natural fiber for a hybrid product). The goal is to have clean, well-separated fibers ready for forming a web.
-
Web Formation: Prepared fibers are then formed into a loose web (sheet) that will become the fabric. Machines like carding machines comb the fibers into a thin, even layer. Sometimes multiple layers are laid on top of each other (through a process called cross-lapping) to build the desired thickness. The result is a fluffy, unbonded mat of fibers arranged mostly randomly but uniformly in distribution. At this stage it looks a bit like a thick, soft batt of cotton.
-
Needle Punching: Next comes the key step – the web is mechanically bonded by needle punching. In a needle-punch machine, thousands of barbed needles repeatedly drive in and out of the fiber web. As these needles penetrate, their barbs catch fibers and entangle them through the thickness of the web. This stitches the fibers together physically without any glue. The process is carefully controlled by parameters like needle density (how many punches per area), needle penetration depth, and needle frequency. By adjusting these, manufacturers can control the fabric’s density, thickness, and strength. The needle punching process is purely mechanical and does not require water, heat, or chemical binders – the fibers are interlocked by the needle action alone, creating a coherent felt-like fabric. This makes needle-punched microfiber fabrics energy-efficient and environmentally friendly to produce (no water waste or chemical pollution). The output of this stage is a raw nonwoven microfiber fabric, often called “felt” or needle-punched cloth, which is strong yet porous.
-
Post-Treatment (Finishing): After needle punching, additional treatments may be applied to enhance performance or handle. One common post-treatment is heat setting or calendering, where the fabric is passed under heated rollers or through an oven to slightly melt and fuse fibers at contact points – this can add strength and control shrinkage. Another is adding a scrim backing or support layer: for example, in high-strength geotextiles, a lightweight woven mesh might be attached to one side to reinforce the fabric. Coatings or saturants can also be applied; for instance, a resin spray to bind the surface fibers more firmly if a stiffer material is needed. Finishing steps can include chemical treatments to impart qualities like water repellency, flame retardancy, or antimicrobial properties, depending on the end-use. As an example, a microfiber leather material (used in car interiors) might be impregnated with a polyurethane resin and then buffed to create a suede-like texture. In other cases, the fabric can be dyed or printed with patterns during finishing. The finishing stage is quite flexible – it can be as simple as cutting the fabric to size and packing it, or as complex as multi-step treatments to laminate layers together. The result of all these steps is a finished microfiber material ready for use in various applications.
It’s worth noting that not all microfiber materials are made by needle punching. Some microfiber textiles are woven or knitted (for example, many high-end microfiber towels are warp-knitted then split to create microfibers). Others are made by spunlace (hydroentanglement), where high-pressure water jets entangle the fibers instead of needles. There are also meltblown microfibers created by extruding and blowing polymers directly into fine fiber webs (commonly used for filtration media like N95 mask filters). However, the needle-punched method described above is widely used for making durable, high-performance microfiber nonwovens used in industries like automotive, geotextiles, and insulation. In our own production facility, we utilize advanced versions of these processes – with modern controls to ensure consistency – as part of our OEM/ODM service. For example, our lines have sensors to monitor fiber distribution and needle wear, helping maintain uniform quality throughout a production run. After manufacturing, every batch undergoes quality checks and is certified to meet relevant standards (ensuring the material is safe, effective, and as specified), reflecting our commitment to efficient, certified manufacturing for our customers.
-
Key Features of High and Low Pile Microfiber
Microfiber materials – whether high pile or low pile – offer a range of attractive features that make them popular in many commercial and industrial applications. Here are some key characteristics:
-
High Strength and Durability: Despite their soft feel, microfiber textiles can be incredibly strong. The production methods (like the needle-punch entanglement or tight weaves) create a fabric that withstands wear and tear. The fibers are firmly interlocked, giving the material good tensile strength and resistance to ripping. For instance, a needle-punched microfiber fabric used in furniture upholstery or car carpeting will hold up under repeated stress without fraying. Even lightweight microfiber wipes can be reused many times because the fibers and bonding are robust. This durability is a big advantage for buyers who need materials that have a long service life, reducing the frequency of replacement.
-
Breathability: Microfiber nonwovens and fabrics are often highly breathable due to their structure. There are many tiny spaces between the fine fibers, allowing air to flow through easily. A high pile microfiber, in particular, tends to be quite porous (since the long fibers create a fluffy structure with air pockets). This is beneficial for applications like filtration (air passes through) and comfort in textiles (fabric doesn’t feel suffocating). For example, microfiber synthetic leather or fabric used in car seats needs to allow some air exchange to avoid trapping heat, and indeed these fabrics can be engineered to be breathable. Even a thick microfiber insulation blanket allows moisture vapor to pass, which helps in applications like outdoor jackets where breathability prevents condensation inside. In short, the high porosity of microfiber materials means they can combine coverage with airflow – a reason they are used in things like breathable medical gowns and athletic wear.
-
Customizability and Versatility: One big benefit of microfiber technology is how tunable it is. Manufacturers can design microfiber fabrics with a wide range of weights, thicknesses, textures, and colors to meet specific needs. For instance, by adjusting pile height, fiber type, or bonding method, you can get a stiff, thick felt for industrial use or a silky, drapable cloth for apparel. Microfibers can mimic the look and feel of other materials too – suede, leather, or even silk – by using special finishing techniques. The material can also be easily colored or printed during production to match branding or design requirements. Additionally, functional additives can be incorporated: for example, copper or silver-infused microfibers for antimicrobial wipes, or carbon-loaded fibers for antistatic performance. This customizability extends to combining layers (laminates) – a microfiber layer could be bonded to foam or film to create a composite with multiple functions. For customers, this means a microfiber supplier can often tailor the product exactly to the application, whether it’s changing the GSM (grams per square meter) of a wipe to adjust its absorbency or choosing a specific fiber blend to balance cost and performance. We frequently work on ODM projects where a partner needs a very specific type of wipe – say, extremely soft for delicate electronics but also lint-free – and microfiber technology allows us to meet those specs by tweaking the fiber and process.
-
Eco-Friendliness: In today’s market, the environmental aspect of materials is crucial. Microfiber nonwovens made by processes like needle-punching have some eco-friendly advantages. For one, the production can be cleaner – as mentioned, mechanical bonding doesn’t require harsh chemicals or lots of water, so it avoids creating polluted wastewater. Modern microfiber fabrics can also be made from recycled polymers (for example, recycled PET plastic bottles turned into polyester microfibers) which gives a second life to waste materials. Some microfiber products are designed to be reusable many times, which reduces single-use waste (consider a microfiber cleaning cloth that replaces dozens of disposable paper wipes). Furthermore, the industry is innovating biodegradable microfibers using biopolymers like PLA (polylactic acid from corn starch) or using natural fiber components, aiming to create products that eventually decompose rather than persist in landfills. That said, “eco-friendliness” also depends on how the product is used – we will discuss environmental considerations in a later section. But from a manufacturing standpoint, microfiber fabrics can certainly align with sustainability goals by minimizing process waste and enabling recycling initiatives.
-
Cost-Efficiency: Microfiber materials can offer excellent cost-effectiveness, especially in large-scale production. Compared to traditional woven textiles, nonwoven microfiber fabrics often have lower production costs because they involve fewer steps and less labor-intensive work. There is no weaving of individual yarns, which cuts down time and expense. The raw materials (polyester, polypropylene, etc.) are generally affordable petrochemical derivatives, and production is highly automated. For buyers, this means you get a high-performance material (strong, absorbent, etc.) at a relatively competitive price. For example, microfiber filtration mats might achieve the same or better performance as a glass-fiber filter but at lower cost and with easier handling. Additionally, because microfibers are effective even in small amounts, lightweight products can be made to do a heavy-duty job – saving material costs. On the whole, when scaling up to industrial quantities, microfiber fabrics provide a good balance of performance per cost unit. This is one reason they are popular in sectors like automotive and construction where cost is as critical as quality. Our own operations leverage efficient manufacturing techniques to keep costs manageable, which in turn lets us offer OEM clients favorable pricing for custom microfiber products without sacrificing quality.
In summary, high and low pile microfiber materials are strong, breathable, adaptable, relatively eco-friendly to produce, and cost-efficient. These features explain why they have become so prevalent in various fields. Next, we will look at exactly where and how these microfiber fabrics are used.
-
Application Areas
Microfiber’s versatility means it finds use in a wide array of industries. Below are some of the primary application areas for high and low pile microfiber materials:
-
Filtration: One of the most important uses of microfibers is in filtration media. Fine microfibers can capture extremely small particles, which makes them ideal for filters in HVAC systems, industrial air filters, vacuum bags, and water or oil filtration units. For example, the high-efficiency filters used in face masks and air purifiers often contain melt-blown microfiber layers that trap dust, aerosols, and even bacteria while still allowing air flow. Needle-punched microfiber felts are also used in liquid filtration – such as filtering sediment from water or oil – because the dense mat of fibers can sieve out contaminants. High pile (lofted) microfiber media can perform depth filtration, trapping particles throughout the thickness of the material, which increases capacity. Low pile or thinner microfiber sheets are used for surface filtration where a very fine screen is needed. The inherent breathability of microfibers (as mentioned earlier) allows filters to have low pressure drop, meaning air or fluid can pass through without requiring excessive energy, all while maintaining high filtration efficiency for tiny particles. Thus, whether in an automotive cabin air filter or an industrial clean-room filter, microfiber technology plays a key role. The fine fibers provide a large surface area to snare particulates, and the strength of the bonded web ensures the filter holds together under flow pressure over time. Many filter manufacturers choose microfiber-based nonwovens to achieve the strict filtration standards in healthcare, automotive, and environmental applications.
-
Geotextiles: Geotextiles are fabrics used in civil engineering and construction, typically for soil stabilization, separation, drainage, or erosion control. Nonwoven needle-punched geotextiles made of polypropylene or polyester microfibers are common in this field. These materials have a felt-like texture and are placed under roads, railroad tracks, or behind retaining walls. The role of a microfiber geotextile is often to allow water or fluids to pass through (preventing water pressure buildup) while holding back soil particles – essentially acting as a soil filter and stabilization layer. The high pile or thickness of some geotextile felts gives them a cushioning effect and high water flow capacity. For example, under a highway, a geotextile layer can help distribute loads and keep different soil layers from mixing, all the while letting rainwater percolate down. Microfiber geotextiles are also used in landfill lining systems and drainage ditches. Their high strength and rot-resistant synthetic fibers make them durable in ground applications, and they resist mold or biological degradation. Because they can be made in very large widths and lengths, installation is efficient for covering big areas. In summary, the combination of permeability and robustness makes needle-punched microfiber geotextiles a go-to solution in construction projects where long-term stability is needed.
-
Automotive Interiors: The automotive industry uses microfiber materials in several ways. Perhaps most visibly, microfiber synthetic leathers and suedes have become popular for car upholstery, headliners (the interior roof lining), door panels, and steering wheel covers. These materials, often made by bonding microfiber nonwovens with polyurethane, offer a luxurious suede-like feel and appearance, providing a high-end look in vehicle interiors. They are also lighter than real leather and can be more durable against heat and fading. High pile microfiber fabrics can appear in cars as well in the form of carpeting or floor mats – their absorbency and ability to trap dirt make them practical for keeping car interiors clean. Additionally, microfiber nonwovens serve as insulation and sound dampening in vehicles. For instance, behind the dashboard or under carpets, there are often thick microfiber felt pads that help reduce noise and vibration from the road or engine. These felts also add thermal insulation, keeping the cabin temperature stable by buffering outside heat or cold. Another automotive use is in cabin air filters (as mentioned in filtration) – ensuring the air passengers breathe is free of pollen and dust, courtesy of microfibers. The automotive sector benefits from microfiber’s versatility: a manufacturer can use a plush, high pile microfiber for a soft seat cover and a dense, low pile microfiber for a door panel insert that needs a smooth finish. With growing focus on sustainability, some car makers are also exploring recycled microfiber materials for interiors. Overall, microfiber textiles contribute to cars that are comfortable, stylish, and high-performance, all while meeting stringent durability requirements (resisting UV light, abrasion from passengers, etc.).
-
Home Textiles: In home furnishings and textiles, microfiber has made a big impact. Many sofas and chairs are upholstered with microfiber fabric that resembles suede – these are appreciated for being easy to clean and resistant to staining (often liquids will bead on the microfiber surface). High pile microfiber throws and blankets are loved for their soft, plush feel and warmth. Because microfibers can be made very fine, they can create extremely soft bedding; for example, some luxury bedsheets and pillow covers are made of brushed microfiber which gives a silky touch. Curtains and drapes sometimes use microfiber fabrics to achieve a good drape with light weight. Additionally, cleaning products in the home are dominated by microfiber: everything from mop pads to multi-surface cleaning cloths. A low pile microfiber cloth is excellent for wiping glass or stainless steel appliances without lint, while a high pile dusting cloth will capture dust effectively. Microfiber towels are also used in kitchens and bathrooms due to their high absorbency – they can soak up spills quickly and dry fast after use. In carpets and rugs, microfiber yarns create soft pile rugs that feel cozy underfoot. The key advantages at home are comfort (soft feel), ease of maintenance, and durability. A microfiber upholstery, for instance, won’t pill or wear out easily and can handle frequent cleaning, which appeals to households with kids or pets. From a B2B standpoint, if you’re a furniture maker or a home goods retailer, using microfiber materials in your products can be a selling point due to these consumer benefits.
-
Industrial Uses: Microfiber materials also find a place in various industrial contexts. One major use is in industrial wipes and cleaning rags. Factories, automotive shops, and electronic assembly plants use microfiber wipes for precision cleaning because the fine fibers can pick up oils, solvents, and microscopic debris very effectively. Low pile microfiber wipes are great for polishing metal components or cleaning glass instruments, as they leave little residue. High pile wipes can soak up chemical spills or apply coatings evenly. In manufacturing, some processes require lint-free environments – microfiber cloths are chosen because they are engineered to minimize lint (especially when edges are sealed). Another industrial application is as absorbent mats or pads. For example, in environmental cleanup or maintenance, microfiber nonwoven pads can absorb many times their weight in fluids, so they are used to contain oil leaks or to wipe down machinery. In automotive manufacturing, large microfiber sheets might be used to cover and protect car bodies between assembly stages (the soft material won’t scratch paint). Additionally, fine microfiber felts are utilized in precision filtration in industrial settings – such as filtering hydraulic fluids or as separators in battery manufacturing – due to their fine particulate capture ability. Microfiber felt belts or rollers are even used in some conveyor systems where gentle yet firm contact is needed to carry products without damage. The industrial realm values microfiber for its combination of softness (won’t damage sensitive parts), absorbency, and strength. We often collaborate with industrial clients to supply specialized wipes and materials that meet rigorous specs, like being silicone-free (for paint shops) or static-dissipative for electronics, showcasing the adaptability of microfiber tech in solving niche industrial challenges.
-
Insulation: Both thermal and acoustic insulation benefit from microfibers. Thermal insulation works by trapping air (since air is a poor conductor of heat), and microfibers excel at this because their dense network creates many tiny air pockets. A well-known example is Thinsulate™ insulation by 3M, used in winter jackets and gloves – it consists of ultra-fine polyester microfibers that trap air and keep warmth in. These microfiber insulations provide warmth equivalent to down or foam but with much less thickness, hence the name “thin-insulate.” In the context of buildings, microfiber-based insulation blankets or panels can be used in walls and attics to provide thermal resistance while being lightweight and mold-resistant. Acoustic insulation is another area: the fine fibers dissipate sound energy effectively. You’ll find microfiber sound-absorbing mats in applications like car cabins (to lessen engine noise), recording studios (as wall panels to reduce echo), or household appliances (like a quiet dishwasher that has microfiber pads to dampen sound). High pile microfiber felts are especially useful here, as their loft can absorb a wide range of sound frequencies. Moreover, microfibers don’t shed dust like some fiberglass insulations do, making them healthier to handle and install. For buyers in need of insulation materials, microfiber solutions can offer a nice blend of performance and ease of use. They can be cut to shape easily, don’t irritate the skin as mineral fibers might, and can be engineered to also resist fire by incorporating flame-retardant fibers. From jackets that keep people warm, to cars that stay quiet, microfiber insulation materials quietly do their job in the background.
-
Packaging: While perhaps not as obvious, microfibers also contribute in the packaging field. High pile microfiber padding can be used to line cases or cartons for delicate instruments, electronics, or glassware. Think of a camera lens case with a soft padded interior – that could be a microfiber plush fabric protecting the lens from scratches and shocks. Some luxury products (watches, jewelry, high-end electronics) come wrapped in a small microfiber cloth or pouch, which both protects the item and can serve to polish it. In shipping applications, microfiber felt liners might protect sensitive components from vibration. There is also exploration into microfiber-based packaging textiles as an alternative to traditional foam peanuts or bubble wrap for sustainable packaging – using pads made of recycled microfiber nonwovens to cushion goods. Because microfiber materials can be made food-safe and lint-free, they can even be used for packaging sensitive medical devices or pharmaceutical products. The packaging sector values the softness and cleanliness of microfiber fabrics: they won’t scratch surfaces and they produce minimal dust. Additionally, the fact that many microfiber materials are reusable or washable means packaging components like divider cloths can be used multiple times (for instance, in automotive component transport between suppliers and assembly plants, reusable microfiber separator sheets protect painted parts). In sum, whether for one-time protective packaging or multi-use transit materials, microfiber provides a gentle but effective barrier.
-
Other Uses: Agricultural Covers and Medical Supplies
Beyond the major areas above, there are some other notable uses of high/low pile microfiber materials:
-
Agricultural Covers: Farms and greenhouses often use nonwoven fabric covers to protect crops, and microfiber-based nonwovens can fulfill this role. These covers (sometimes called crop covers or frost blankets) are lightweight sheets spread over fields to shield plants from cold temperatures, pests, and heavy rain. Microfiber crop covers made of polypropylene or polyester allow sunlight and air to penetrate while providing a barrier against insects and retaining some warmth near the plants. Because they are porous, they won’t suffocate the crops – moisture and air can still circulate. They help create a microclimate that can improve germination and growth early in the season. High pile isn’t necessary here; typically a thin, low-pile spunbond or lightweight needle-punched microfiber works, focused on being breathable yet protective. Another agricultural use is in root bags or containers made of needle-punched microfiber felt, which promote healthy root pruning for trees and plants (the microfibers let roots breathe and excess water drain out). Also, silage covers or wraps for bales can use microfiber-reinforced sheets to provide strength and tear resistance. The advantage of microfibers in agriculture is their weather resistance and light weight – they are easy to deploy over large areas and can last through a growing season (or be engineered to biodegrade after a certain time, eliminating waste). These materials help farmers reduce reliance on chemical pesticides (since the physical barrier keeps many bugs out) and mitigate weather risks, which is increasingly valuable.
-
Medical Supplies: The medical and hygiene field is a huge consumer of nonwoven microfiber materials. A prime example is surgical face masks, which typically have a middle layer made of melt-blown microfibers acting as the filter to block pathogens. The outer and inner layers are often spunbond microfibers. This combination yields a mask that is effective in filtration and also breathable. Similarly, surgical gowns and drapes are often made from SMS (spunbond-meltblown-spunbond) nonwoven fabric, where microfibers provide a barrier to liquids and microbes. The fine fibers in these materials are critical to achieving the necessary protection levels (like resisting blood penetration) while remaining relatively comfortable to wear for doctors and nurses. Wound dressings and bandages sometimes incorporate microfiber layers for absorbency – for example, a composite dressing might include a microfiber pad to suck up exudate from a wound. Sterile wipes and pads for hospitals are frequently microfiber because they can clean sensitive equipment without leaving lint, and they can even remove bacteria from surfaces more effectively than cotton (microfibers can pick up microbes mechanically). High pile microfiber cloths are used in some medical cleaning contexts to trap dust and pathogens (color-coded microfiber cloths for different hospital zones are now common for infection control cleaning). Another area is laboratory filters and membranes – fine microfiber nonwovens serve as filters in things like blood filtration, drug purification processes, or even as the separation layers in diagnostic devices. The medical field values the hygiene and performance of microfibers: the fact that these fabrics can be made sterile, are often single-use (preventing cross-contamination), and can be engineered to have specific properties (e.g., alcohol-resistant gown material, or antiviral coatings on mask fibers). During the recent global health events, the demand for medical microfiber nonwovens surged due to the need for high-quality PPE (personal protective equipment), underscoring how vital this material is for healthcare. In our business, we supply functional wet wipes and other hygiene products – many of which rely on microfiber nonwoven substrates – so we pay special attention to meeting medical-grade standards for these uses (such as ISO 13485 or FDA compliance when required).
-
Advantages and Limitations
Microfiber materials, as we’ve seen, have many advantages that make them attractive for diverse applications. However, like any material, they also have limitations or trade-offs. In this section, we discuss both sides in terms of functionality, durability, environmental impact, tactile feel, and cost.
-
Multifunctionality and Versatility (Advantage): A clear advantage of microfiber is its multifunctionality. A single microfiber fabric can often serve multiple purposes. Take a microfiber wipe: it not only cleans surfaces, but can also absorb oils, pick up bacteria, and dry quickly – all in one. Microfiber nonwovens can be designed to be waterproof yet breathable, or strong yet elastic, depending on needs. This kind of material flexibility means one product can replace several traditional products. For a business, that means simplifying supply chains – for example, a particular microfiber fabric in a car might provide sound insulation, cushion, and filtration simultaneously, reducing the need for separate layers. The ability to integrate features (like making a fabric flame-retardant, or electrically conductive for static dissipation) adds to this multifunctionality. Manufacturers can imbue microfiber textiles with smart additives or coatings, so the material can do more than just the basic function of covering or filtering. This versatility is a significant upside; it enables innovation in product design. From our experience, when a client comes with a problem (say, they need a material that is thin but very warm and moisture-wicking), a microfiber-based solution can often be crafted to tick all the boxes. Traditional materials might not handle such combined requirements as elegantly.
-
Durability (Advantage): Durability is another strong point for most microfiber materials. Since the fibers are synthetic (often polyester or nylon), they resist biodegradation and can endure stress. They don’t rot or mildew easily, and insects don’t eat them (unlike natural fibers like cotton or wool). Microfiber fabrics maintain integrity even after repeated washing or use. High-quality microfiber towels, for instance, can be laundered hundreds of times before showing wear. In industrial uses, a needle-punched polypropylene microfiber geotextile buried in soil can last decades maintaining its function. This durability makes microfiber products cost-effective in the long run and reliable in critical uses. However, durability has a flipside: because the materials are so long-lasting, discarded synthetic microfibers persist in the environment. We’ll touch on that under environmental aspects. Another minor limitation related to durability is heat: most microfiber (being plastic-based) will melt or deform at high temperatures (e.g., direct contact with a very hot surface or ironing on high heat). They generally can’t withstand as high temperatures as some natural or specialty fibers. So, while a microfiber cloth is great for cleaning, you wouldn’t use it in an extremely hot environment (above its melting point). In normal use cases, though, this is rarely an issue. Overall, durability is a big plus for producers and end-users – products last longer and perform consistently, which is a mark of quality we strive for. We ensure our manufacturing processes (and any stitching or assembly for finished goods) maximize the inherent durability of the material so that the end product can handle the stresses of its intended use.
-
Environmental Aspects (Advantage & Limitation): The environmental impact of microfibers is a nuanced topic. On one hand, as mentioned, the production of nonwoven microfiber fabrics can be quite eco-efficient (low waste, no harmful effluents, etc.), and using recycled input reduces the reliance on virgin petrochemicals. The fact that microfiber products can be reused many times (a microfiber cleaning cloth can replace hundreds of disposable wipes) is an environmental advantage in terms of reducing waste. Additionally, lighter materials in cars or planes improve fuel efficiency – so if microfiber components lighten a vehicle, they indirectly cut carbon emissions. However, there are notable environmental concerns too: microfiber pollution. Because microfibers are plastic-based, when they do shed or eventually get thrown away, they contribute to microplastic pollution. Tiny fibers can slough off during washing of textiles and end up in waterways. Studies have found that synthetic microfibers from laundering clothes are a significant source of microplastics in the ocean. These particles are so small that they pass through many filters and can accumulate in marine life. This is a limitation and a growing regulatory concern. As a result, the textile industry is actively seeking solutions, such as filters in washing machines, or developing fibers that biodegrade. Another environmental limitation is end-of-life disposal: most synthetic microfibers are not biodegradable (unless made of special biopolymers). They will sit in a landfill indefinitely. Recycling of microfiber material is possible (e.g., melting down polyester), but if the material is contaminated or a composite, it can be hard to recycle in practice. The industry trend is to address these issues by innovating more sustainable microfibers. For instance, some companies are now producing biodegradable polyester that can break down faster, or mixing natural fibers (like Tencel or cotton) to give a microfiber fabric a more biodegradable profile. There’s also a push for regenerative or circular approaches – where used microfiber products are collected and recycled back into new fibers. In summary, while microfiber technology offers environmental upsides in use and production efficiency, it also poses challenges at the end of its life cycle. As responsible manufacturers, we acknowledge these limitations and are actively supporting solutions, such as using recycled raw materials and participating in research on fiber biodegradability, to ensure microfiber products can be part of a sustainable future.
-
Touch and Feel (Advantage & Limitation): The tactile feel of microfiber fabrics is often cited as a major advantage. They can be extremely soft to the touch – think of a high-pile microfiber blanket or a microfiber leather jacket that feels supple. Microfibers can create textures from silky-smooth to velvety to plush, giving designers a lot of options for achieving a desired hand-feel. Consumers generally find microfiber clothing and bedding to be comfortable (smooth on the skin, with no scratchiness). In cleaning, the soft texture is gentle on surfaces, which is great for not scratching paint or glass. However, not everyone likes the feel of microfiber; some people find that a very fine microfiber cloth can cling to dry skin (because of the micro hooks of fiber catching on skin imperfections). That sensation can be a bit unpleasant to some. Also, compared to natural fibers like cotton, microfiber can feel less “breathable” in certain apparel uses if the fabric is very tightly woven (it might trap more humidity, causing a clammy feel in hot weather). But this is mitigated by designs that incorporate ventilation or by blending with moisture-wicking fibers. Another aspect is static electricity – synthetic microfibers can build up static charge, especially in low humidity, which can make them cling or spark slightly when taking off a garment. Treatments can reduce this (antistatic finishes). From a limitation standpoint, one could say that microfiber lacks the organic feel that some natural textiles have; for instance, high-pile polyester fleece versus a wool sweater – they feel different, and some may prefer the natural fiber feel. Nonetheless, for most applications, the ability to engineer the touch and feel (whether ultra-soft for a baby blanket or a grippy texture for a cleaning cloth) is a net positive. In our product development, we pay close attention to tactile quality – a wipe that feels too rough or too slippery can reduce user satisfaction, so we adjust fiber fineness or finishing processes to get the right feel for the intended use.
-
Production Cost and Economic Factors (Advantage & Limitation): We’ve touched on cost efficiency as an advantage. Microfiber materials can be produced at scale with relatively low unit costs, making them economical for businesses to adopt. Especially for disposable or high-volume products (like hygiene wipes or mask filters), nonwoven microfibers are the go-to choice to keep costs in line while meeting performance needs. However, it’s worth noting some limitations here: the cost of raw materials (polypropylene, polyester) is tied to global oil prices, so there can be volatility. If oil prices spike, synthetic fiber prices may rise accordingly, which can tighten margins for manufacturers and buyers. Additionally, setting up advanced microfiber production (like a state-of-the-art meltblown line or needle-punch line with high output) requires significant capital investment in machinery. For a smaller operation, this might be a barrier, meaning not everyone can easily produce at the lowest cost – there is some economy of scale at play. When extremely high quality or specialized microfiber is needed (for example, a unique microfiber with conductive properties or medical-grade cleanroom production), the costs can be higher than standard textile manufacturing due to technology and quality control requirements. In contrast, commodity textiles like basic woven cotton might be cheaper for certain simple uses if high performance isn’t required. So while generally microfiber delivers great value, it’s not always the absolute cheapest option if an application could use a very basic material instead. From an OEM standpoint, we consider both cost and performance – often educating clients that while a microfiber solution might cost slightly more than a low-tech alternative, it often pays off in performance gains or longevity. In many cases, the cost difference has narrowed significantly as technology has matured. The continued innovation and scaling in this industry promise to keep costs competitive. In fact, many emerging markets and industries are adopting microfiber solutions precisely because improvements in manufacturing have made them cost-effective where they weren’t a couple of decades ago.
In weighing advantages and limitations, it’s clear that microfiber (high or low pile) is a high-performance material with few downsides for most uses. The main caveats revolve around environmental impact and ensuring the right choice of fiber or finish for a given task (to avoid issues like static or breathability problems). Being aware of these factors allows manufacturers and buyers to mitigate them – for example, using liners with microfiber apparel to enhance comfort, or implementing recycling programs for used products. As a manufacturer, my philosophy is to maximize the benefits (through smart design and quality control) and minimize the drawbacks (through innovation and responsible practices), so that our partners get the best of what microfiber technology can offer.
-
Market Outlook and Trends
Global nonwoven fabrics market is projected to grow from around USD 39.8 billion in 2021 to USD 57.9 billion by 2027, reflecting an approximate 6.5% annual growth rate. This steady growth is driven by rising demand across industries like automotive, healthcare, and filtration, as well as continuous product innovation.
The market for microfiber and related nonwoven fabrics continues to expand robustly. Buyers are increasingly seeking advanced materials that give them an edge, and microfiber fits that bill in many cases. Several key trends are shaping the high/low pile microfiber landscape as we move forward:
-
Improvements in Functionality: Research and development efforts are constantly pushing microfiber materials to new heights. One trend is the development of smart or functional microfibers – textiles that do more than just the basic function. For instance, we now see microfiber fabrics that incorporate electronics for sensing (e.g., a window wipe that can indicate when a surface is truly clean, using some reactive fibers), though such products are in early stages. More common are enhancements like antimicrobial finishes (especially important after the global pandemic – there’s higher interest in wipes and towels that can kill germs on contact) and flame-retardant or UV-resistant additives for industrial fabrics. Another area of improvement is making microfibers that mimic natural fibers even more closely in comfort but surpass them in performance. High pile microfiber blankets that breathe like cotton but insulate better, or microfiber synthetic leather that equals real leather in appearance yet is more durable, are examples. Nanotechnology is also being applied – creating even finer nanofibers for filtration of viruses and extremely small particles, which can be layered with slightly larger microfibers to create gradient filters with very high efficiency. The combination of different fiber scales and materials leads to composite nonwovens that offer multi-functionality (for example, a 3-layer microfiber structure in a single material – one layer might absorb, one might filter, one might provide strength). For buyers and product developers, these improvements mean new application possibilities and better performance in existing uses. Product innovation is specifically cited as a driver of market growth, with developments like smart nonwoven fabrics contributing to future demand. In our company’s R&D, we keep a close eye on these advancements – partnering with textile institutes to experiment with new fiber blends and finishes – so that we can offer our clients state-of-the-art material options in their OEM products.
-
Sustainable Materials and Practices: Sustainability is arguably the biggest trend across all manufacturing, and microfiber textiles are no exception. There is a strong push toward greener microfibers – both in content and production. On the material side, this includes increased use of recycled fibers (for example, recycled PET from bottles is being used to make microfiber cleaning cloths, catering to customers who want recycled content). It also includes exploring bio-based fibers: companies are looking at polyamides derived from castor oil, or polylactic acid fibers from plant sources, to create microfiber fabrics that reduce dependence on fossil fuels. Moreover, regenerative fibers and biodegradable microfibers are under development to tackle the microplastic pollution issue. Industry leaders recognize that addressing synthetic microfiber pollution at the source is critical. This means designing fibers that either don’t shed as much or that safely break down if they do enter the environment. For instance, one trend is seaweed or cellulose-based microfibers that can dissolve harmlessly over time. On the production practice side, sustainability involves minimizing waste and energy usage in factories. Many nonwoven manufacturers are now implementing ISO 14001 environmental management systems and optimizing processes to use less electricity and heat. There’s also interest in life-cycle analysis – providing customers with data on the carbon footprint of the microfiber materials they purchase. Initiatives like textile recycling programs are becoming more common: used microfiber products (like discarded garments or old car upholstery) can be collected and processed back into fiber or shredded for other uses, contributing to a circular economy. As a manufacturer, we have embraced sustainable practices by obtaining relevant certifications and improving efficiency (for example, optimizing our water reuse in any finishing processes, and using solar energy for part of our factory power). We anticipate that in marketing to end-users, our clients will increasingly highlight the eco-friendly aspects of the materials – so we strive to give them positive stories to tell, such as “this cleaning cloth is made from 50% post-consumer recycled fiber” or “this synthetic leather is free of harmful solvents.” Governments and large corporations are also starting to prefer suppliers who can meet sustainability criteria, so being ahead on this trend is not just good for the planet, but good business strategy.
-
Smart Manufacturing and Industry 4.0: On the production side, the trend of Industry 4.0 and smart manufacturing has taken hold in the textile and nonwoven industry. This means factories are becoming more automated and digitally integrated. For microfiber production, modern equipment now comes with a plethora of sensors and IoT connectivity. These sensors monitor parameters like fiber distribution, web uniformity, needle wear, temperature, humidity, and more in real time. The data collected is analyzed using software and sometimes AI to ensure optimal machine performance and product quality. For example, advanced needle-punching lines might adjust speed or needle frequency automatically if sensors detect a density variation, thus correcting any inconsistencies on the fly. Machine learning algorithms can predict when a filter in a meltblown line will clog or when a needle board needs maintenance, allowing preventative care and reducing downtime. Real-time monitoring helps maintain consistent quality – a critical factor for clients who demand reliability. Automation has also increased throughput and efficiency; tasks that used to require manual intervention are now handled by robotic systems (for instance, fabric roll changes, packaging, or quality inspection via camera systems). All of this contributes to better scalability and repeatability. A notable aspect of Industry 4.0 is the focus on data: production data is being used to improve processes continuously. As one machinery maker described, adding more sensors and using cloud analytics can turn a wealth of production data into actionable intelligence for improving quality and energy efficiency. In our operations, we have moved towards these smart manufacturing practices as well. We utilize an MES (Manufacturing Execution System) that tracks each order through the factory, ensuring traceability. If a client ever has a question or issue, we can pinpoint exactly which batch of fiber and what machine settings were used, which greatly speeds up troubleshooting and reinforces trust. Embracing smart manufacturing also means we can handle complex custom orders with precision, because the machines can be finely tuned and monitored. For buyers, this trend means they can expect more consistent quality, faster turnaround times, and often better pricing due to efficiency gains. It also means greater transparency – some clients even have portals to see production status of their orders in real time, which is a level of supply chain integration that was not possible in the past.
-
Market Growth and Global Trends: The market outlook for microfiber and nonwoven fabrics remains very positive. As illustrated in the chart above, nonwoven fabrics (which include many microfiber-based products) are projected to grow significantly in the coming years. A CAGR of around 6.5% through 2027 is anticipated. The growth is fueled by several factors: the expansion of industries like automotive (where there’s an increasing use of lightweight nonwoven components for fuel efficiency), healthcare (growth in disposable medical products and hygiene awareness), and an overall trend of replacing traditional materials with technical textiles for performance or cost benefits. Geographically, Asia (especially China) continues to be a major driver of production and consumption, given its large manufacturing base and infrastructure projects. We see continuous investment in new nonwoven plants in the region. Meanwhile, in Europe and North America, there’s a push for higher-value specialized nonwovens (such as smart textiles or eco-friendly textiles) where companies can differentiate. Another global trend is partnerships and consolidation: to meet demand and innovate, companies are collaborating – like chemical companies working with fiber producers to develop new polymers for microfibers, or nonwoven producers acquiring smaller specialty firms to broaden their portfolio. For buyers, this means more options will be available on the market, but also the need to choose reliable partners. With so many products, ensuring you get what meets your specifications is key – which is why due diligence like checking certifications, visiting factories (even if virtually), and starting with pilot orders is advisable. On our side, as a China-based OEM/ODM supplier, we position ourselves to be at the intersection of these trends: adopting new technologies, committing to sustainability, and scaling our production to meet global demands quickly. We find that buyers today value not only price and quality but also the innovation capacity and credibility of the supplier. Thus, we actively communicate how our microfiber products incorporate the latest best practices and how our facility meets international standards (for quality management, social compliance, etc.). The professional network we maintain with industry experts and associations helps us stay ahead of market trends, which in turn benefits our partners who can trust us to bring them up-to-date solutions.
In conclusion, high and low pile microfiber materials have proven themselves as indispensable in the modern B2B landscape. They combine performance with flexibility, allowing businesses to create better products across cleaning, filtration, textiles, and beyond. The manufacturing technologies ensure that we can produce these materials efficiently and in an eco-conscious way. As we look to the future, ongoing improvements in material science, sustainability, and smart manufacturing are set to further enhance what microfiber can do. In the spirit of ELBERT’s company values – innovation, quality, and partnership – we will continue to champion these advances, working closely with our global partners and clients to apply microfiber solutions that drive success for all parties involved. Whether you are a reseller looking to expand your product line with high-performance microfiber towels, or an OEM client designing the next automotive interior, understanding the nuances of high vs low pile microfiber and the industry trends will help you make informed, forward-thinking decisions. We’re excited to be part of this journey, leveraging our expertise to support your business needs in the world of microfiber.
Elbert Zhao
Founder, ELBERT Wipes Solutions
📧[email protected] | 🌐 www.elbertwipes.com
8 production lines | 22 processing lines | OEKO-TEX certified | Walmart-approved supplier