Car Wipes
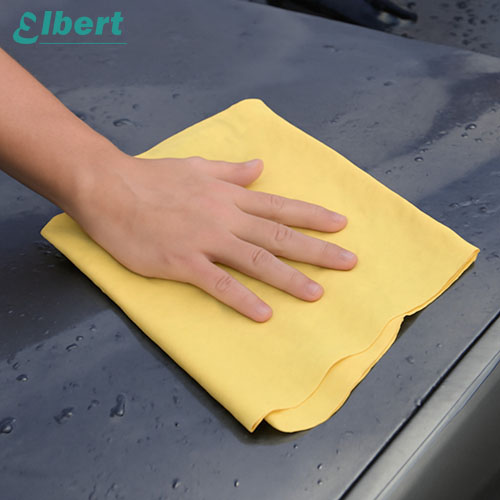
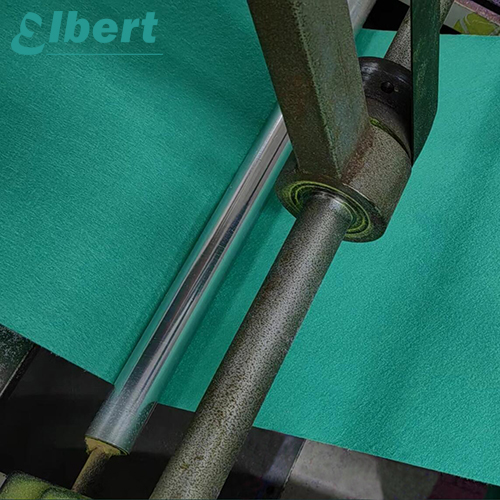
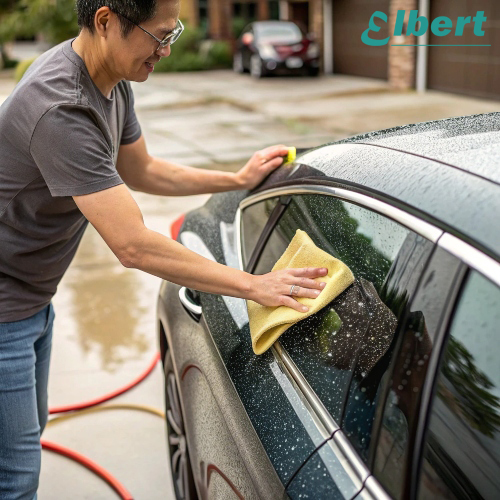
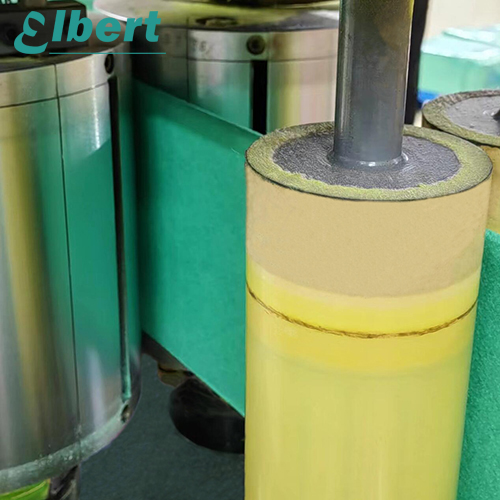
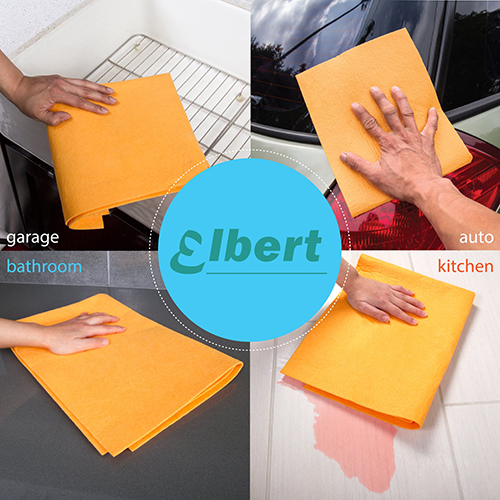
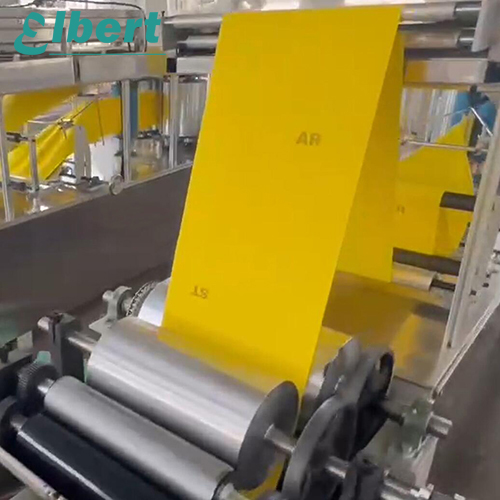
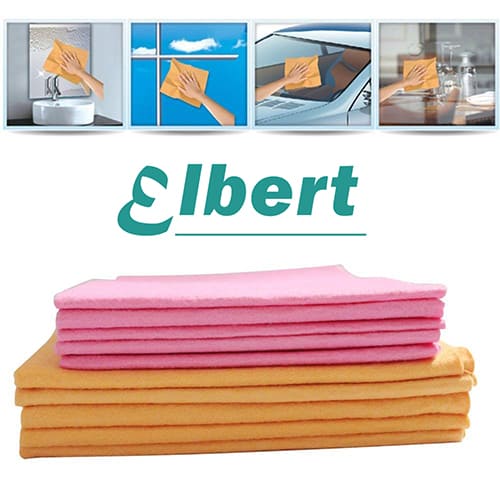
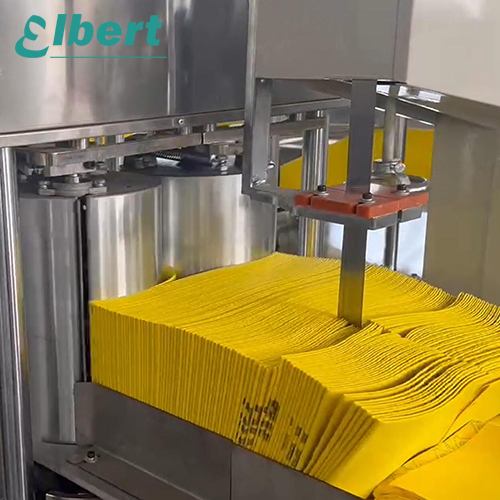
Car wipes a type of nonwoven fabric material commonly used for cleaning and maintaining automobile interiors, as well as for many other purposes in various industries. Unlike traditional woven cloths, nonwoven car wipes are made by bonding fibers together directly into a sheet or web, without weaving or knitting. This gives car wipes unique characteristics that make them popular in both consumer and industrial settings. In this article, we take a broad look at car wipes – how they are manufactured, their key features, where they are used, other innovative uses, their advantages and limitations, and current market trends. The aim is to provide a balanced, educational overview in clear language, suitable for technical readers and industry professionals who want to understand the car wipes (nonwovens) industry.
Manufacturing Process
The manufacturing of car wipes typically involves a nonwoven production process. One common method is needle-punching, a mechanical process used to bond fibers into a cohesive fabric without knitting or weaving. The overall production can be broken down into several stages:
-
Fiber Preparation – Raw fibers (which can be natural like cotton or synthetic like polypropylene) are prepared by cleaning and blending. The fibers may be a mix of types to achieve certain properties. The goal is to have individualized fibers ready for forming the web.
-
Web Formation – The loose fibers are laid out into a continuous web (sheet) using machines like carding machines or air-laying systems. The carding machine combs and orients the fibers, spreading them into an even web structure. Multiple layers of web can be stacked to reach the desired thickness.
-
Needle Punching – The fiber web is then strengthened by needle punching. In this step, a bed of barbed needles repeatedly punches through the fiber web, entangling the fibers as the web moves through the machine. This entanglement bonds the fibers mechanically and forms a stronger, felt-like fabric. The density and strength of the material can be controlled by adjusting needle parameters (number, depth, and punch frequency).
-
Finishing – After needling, the material may undergo finishing treatments. This can include adding a lightweight backing (scrim) for additional support or applying coatings (for example, to make it more durable or absorbent). Finishing might also involve cutting the fabric into wipes of desired size, and packaging if it’s a consumer product.
Schematic diagram of a needle-punching process: barbed needles (mounted on a needle board) repeatedly penetrate the fiber web to entangle fibers and bond the material into a fabric. This mechanical action condenses the loose fiber web as it moves from the feed end to the delivery end, producing a needle-punched nonwoven fabric. Modern needle-punching machines contain many needles and can punch the web thousands of times per minute to ensure consistent bonding.
The needle-punching method described above is purely mechanical and does not require added chemicals or heat during bonding. This makes it relatively eco-friendly and energy-efficient compared to some other fabric-making processes. In fact, needle-punched nonwovens can retain nearly 100% of the raw fiber material in the final product (since no solvent or water washes fibers away), and the resulting fabric can often be recycled or reused if the fiber type allows. Besides needle punching, other bonding methods (like thermal bonding or hydroentangling with water jets) can also be used to make nonwoven wipes, but the end goal is the same: to create a strong fabric directly from fibers.
Main Features
Car wipes (and nonwoven fabrics in general) have several important features and properties that distinguish them from traditional textiles. Here are some of the main features of needle-punched nonwoven wipes:
-
High Strength and Durability: Despite being lightweight, nonwoven car wipes can be made very strong and resistant to tearing. The mechanical entanglement of fibers gives the material high tensile strength for its weight. Many wipes can withstand scrubbing and frequent use without disintegrating. This durability makes them suitable for both disposable wipes and more robust applications.
-
Breathability: Nonwoven wipes can be engineered to be breathable or porous. The needle-punch process creates a fibrous network with tiny pores, allowing air to pass through while still holding together. For example, some car wipes and cleaning cloths are designed to absorb water but also dry out quickly thanks to this breathability. (In contrast, nonwovens can also be made water-resistant when needed by adding coatings, showing their adaptability.)
-
Customizability (Versatility): Nonwovens are highly customizable in terms of thickness, texture, composition, and treatments. Manufacturers can choose different fiber types (polyester, cotton, viscose, etc.) or blends and adjust the production parameters to achieve the desired properties. For instance, a wipe can be made softer for delicate surfaces or more abrasive for tough cleaning. Colors and patterns can be added, and additional features (like embossing or printing) can be introduced easily. This versatility allows car wipes to be tailored for specific needs.
-
Eco-Friendliness: Many modern nonwoven fabrics emphasize eco-friendly aspects. They can be made from recycled fibers or biodegradable materials, and the production process can have a lower environmental footprint than woven fabrics. For example, some disposable car wipes use bio-based fibers or wood pulp that breaks down more easily after use. Additionally, because nonwovens do not require intensive weaving, they often consume less energy and produce less waste in manufacturing.
-
Cost Efficiency: Nonwoven car wipes are generally cost-effective to produce at scale. The production process is streamlined and faster than traditional weaving, translating into lower unit costs. For buyers (like automotive businesses or cleaning companies), these wipes offer an economical option compared to woven cloths. The ability to produce large rolls of nonwoven fabric and then cut them into wipes of various sizes means high productivity. Overall, the combination of inexpensive raw materials (e.g. polypropylene) and efficient manufacturing makes car wipes a budget-friendly choice.
Application Areas
Car wipes might sound specific to automobiles, but the underlying nonwoven material finds use in a wide range of application areas. Here we highlight several key application domains for needle-punched nonwovens (including but not limited to car wipes):
-
Automotive Interiors: Nonwoven fabrics are extensively used in cars and other vehicles. Apart from disposable cleaning wipes for dashboards and glass, needle-punched materials show up in the vehicle itself – for example, as carpet backing and floor mats, trunk liners, cabin air filters, and insulation padding. The high strength and moldability of nonwovens allow them to be formed into door panel trim or headliner insulation. In car carpets, nonwoven backing provides durability and helps the carpet conform to the car’s shape. Similarly, trunk liners made of needle-punched felt protect the trunk and can be made lightweight yet tough. Even some filters in the car (like air and oil filters) use nonwoven media to trap particles.
-
Industrial and Manufacturing Uses: In industrial settings, nonwoven materials serve as shop wipes and cleaning cloths for equipment because of their absorbency and strength. They are also used in geotextiles and construction: heavy-duty needle-punched nonwovens act as liners and covers in civil engineering (for soil stabilization, erosion control, drainage, etc.). For example, a thick needle-punched fabric might be laid under a road or railway to stabilize the ground (a use case for nonwoven insulation and separation layers). Their ability to filter and allow water flow (while holding soil back) makes them ideal for such applications.
-
Home and Institutional Cleaning: Nonwoven wipes are ubiquitous in home cleaning supplies. From kitchen wipes and floor wipes to polishing cloths, these products are essentially the same technology as car wipes. They are valued for being lint-free and able to absorb spills well. In homes, you’ll find nonwoven dusting cloths and disposable disinfectant wipes. In places like hospitals or schools, nonwoven cleaning wipes are used for their one-time-use hygiene (e.g. sanitizing surfaces). Their cost-effectiveness allows widespread use and easy disposal when contaminated.
-
Packaging and Protective Covers: Nonwovens are used in certain packaging applications, especially where a breathable or cushioned material is needed. For instance, some delicate products or equipment might be wrapped in a nonwoven fabric to protect against scratches while allowing air circulation. In medical packaging, a nonwoven wrap is used to allow sterilization gas to penetrate (due to porosity) and then keep contents sterile. Reusable shopping bags made from nonwoven polypropylene are another example of packaging – they are lightweight but strong, illustrating how a “car wipe material” can be fashioned into a sturdy bag.
-
Filtration: One of the biggest application areas for nonwovens is filtration. The random fiber web structure can trap particles effectively while still letting fluids or air pass through. Needle-punched felts and other nonwoven filters are used in air filters, oil filters, water filters, and HVAC systems. In cars, as mentioned, the cabin air filter often uses a nonwoven media to catch dust and pollen. Industrially, many filter presses and vacuum filters use nonwoven cloth. The ability to fine-tune pore size by adjusting fiber and needle density means filters can be made for different efficiency levels (from coarse particle filters to HEPA-grade filters).
-
Insulation (Thermal and Acoustic): Nonwovens also find use as insulation materials. In buildings and automotive interiors, thick needle-punched mats serve as sound insulation and thermal insulation layers. For example, under a car’s hood or behind door panels, nonwoven mats deaden sound and reduce vibration (as acoustic insulation), making the cabin quieter. Similarly, they can provide a layer of thermal insulation (as seen in some winter jackets or sleeping bags that use needle-punched batting). Such insulation materials are lightweight, and because they are fiber-based, they trap air effectively to slow heat transfer. Nonwoven insulation is also used in appliances (like as a sound dampening layer in a washing machine or refrigerator).
As the above list shows, the humble nonwoven fabric extends far beyond just “wipes.” Its applications range from everyday household items to critical components in cars, buildings, and industrial systems. This is a testament to the versatility of the material.
Other Uses
Beyond the common application areas mentioned, there are other interesting uses of nonwoven fabrics related to car wipes:
-
Agricultural Covers: Nonwoven fabrics are widely used as agricultural crop covers and landscape fabrics. These agricultural covers (often made of spunbond or needle-punched polypropylene) protect crops from frost, heavy rain, hail, and pests. Farmers drape lightweight nonwoven sheets over fields to create a microclimate that shields plants from extreme weather while still letting water and air through. Because of their breathability, these covers allow sunlight, air, and moisture to reach the plants but reduce evaporation and thermal radiation loss at night, thus preventing frost damage. By using such covers, the need for chemical pesticides can also be reduced, supporting more organic farming practices. Nonwoven mulch fabrics are another agricultural use – they let water permeate soil but block weeds.
-
Medical Supplies and Healthcare: The medical field relies heavily on nonwoven materials. Many medical supplies that are disposable are made of nonwoven fabric: surgical masks, isolation gowns, caps, shoe covers, surgical drapes, wound dressings, and even certain bandages. Car wipes and medical wipes share this technological base. In medical settings, nonwovens are favored because they can be made sterile, they filter bacteria and viruses, and they are single-use (which prevents cross-contamination). For example, a surgical gown made of spunbond-meltblown nonwoven provides a barrier to fluids and germs, and after one use it is disposed of to ensure no pathogens are transmitted. The safety and hygiene advantages are significant – nonwovens don’t shed lint like woven textiles (important in wound care and electronics assembly), and they can incorporate special treatments like anti-bacterial or fluid-repellent coatings for extra protection.
These other uses demonstrate the broad impact of nonwovens. A technology used for a car cleaning wipe might also be protecting vegetables in a field or safeguarding a surgeon in an operating room. The material’s ability to fulfill very different needs by slight modifications in manufacturing is part of what makes nonwovens a “silent hero” in many industries.
Advantages and Limitations
Car wipes (nonwoven fabrics) come with a set of advantages that explain their widespread use, but they also have some limitations to consider. Below is a quick overview of key advantages and limitations:
Advantages | Limitations |
---|---|
Durable for its weight: Nonwoven wipes can be very strong and hold up to scrubbing and use. | Limited longevity: Compared to woven cloth, nonwovens can have lower overall durability for long-term use. Many cannot be washed and reused repeatedly like traditional fabrics. |
Versatile and customizable: Properties (thickness, softness, absorbency, etc.) can be tailored during manufacturing to suit different applications. | Prone to tearing in one direction: Fibers may be preferentially oriented, so the material might tear more easily at certain angles (manufacturers work on improving this). |
Cost-effective production: Fast, high-volume manufacturing leads to low cost per unit. | Environmental impact if not managed: Most car wipes are made of synthetic fibers (polypropylene, polyester) derived from petroleum. If disposed improperly, they can contribute to plastic waste since they biodegrade slowly. |
Absorbent and lightweight: Excellent for tasks like cleaning spills; easy to handle and carry. | Feel and comfort: Nonwovens can lack the comfort of woven textiles. For example, a nonwoven cloth may feel stiffer or less “breathable” on skin compared to cotton, which can matter for wearables or linens. |
As shown above, one of the major advantages of car wipes is their strength-to-weight ratio – they perform well in cleaning tasks and industrial uses without needing a heavy, thick cloth. Their customizability and low cost are also big plus points, enabling single-use products that are economically feasible. Additionally, nonwoven wipes can be very absorbent (depending on fiber blend), making them ideal for cleaning oil, water, and other fluids.
On the other hand, a notable limitation is that nonwoven fabrics generally do not match the longevity of woven fabrics. A cotton towel can be washed and reused hundreds of times, whereas many nonwoven wipes are intended for limited use or single use. In fact, nonwovens in pure form are often not wash-durable – agitation and heat in a washing machine might cause them to disintegrate or lose structure. The fibers are bonded by entanglement or adhesive rather than interlaced yarns, so repeated stress or bending can eventually make them fuzz up or tear. For this reason, car wipes are usually considered disposable or semi-disposable items.
Another concern is environmental impact. Traditionally, a lot of nonwoven wipes are made from polypropylene, which is a plastic. If these wipes are littered or end up in landfills, they can persist for a long time (though polypropylene is said to degrade faster than some other plastics, it still takes years). The rise of nonwoven disposable products – from wet wipes to surgical masks – has raised sustainability questions. On the positive side, efforts are underway to produce more biodegradable or recyclable wipes, using fibers like viscose (rayon) or polylactic acid (PLA) that have a smaller environmental footprint. The industry is aware that the “disposable nature” of nonwovens is a double-edged sword: great for hygiene and convenience, but potentially problematic for waste management.
In terms of the feel of the material, advances have been made to make nonwovens softer and more cloth-like (for example, adding a soft finish or using finer fibers). Many car wipes are indeed quite soft to the touch. However, very smooth or silky textures (like those of high-thread-count cotton or microfiber weaves) are harder to achieve. For most cleaning applications this isn’t a big issue, but it means nonwovens are less common in, say, fashion apparel where comfort against skin is paramount.
Overall, the advantages tend to make nonwoven car wipes the go-to choice for convenience and functionality, while the limitations remind users and manufacturers to choose the right tool for the job and to innovate for sustainability.
Market and Trends
The market for car wipes and related nonwoven materials has been growing globally, driven by their utility and the demand for convenient cleaning solutions. In recent years, especially during the COVID-19 pandemic, the wipes market saw a significant surge as cleaning and sanitizing products were in high demand. The global nonwoven wipes market (which includes car interior wipes, personal care wipes, industrial wipes, etc.) was valued at around $23–24 billion in 2022. After a slight post-pandemic correction, it is forecast to resume steady growth with an expected market value exceeding $30 billion by the end of the decade (around 2029). This corresponds to an estimated annual growth rate of about 6%, reflecting strong and sustained interest in wipes products worldwide. The growth is fueled by multiple sectors – consumer cleaning wipes, healthcare and hygiene products, automotive and industrial uses – all of which are expanding. Developing regions are also contributing to higher demand as disposable income rises and the preference for disposable convenient products increases.
A clear trend in the market is a shift toward more eco-friendly and sustainable materials. As noted, there are sustainability concerns with traditional synthetic wipes (they can create environmental pollution if disposed of improperly). In response, manufacturers are investing in “greener” nonwovens – for example, using bio-based fibers (like plant-based polymers or recycled cotton) and developing biodegradable wipes that will break down faster after use. Some companies have introduced car wipes made from bamboo fiber or blends that are compostable. Others are focusing on recyclable wipe products or enabling easier collection and recycling of used wipes. The push for sustainability also includes reducing the carbon footprint of production, so more efficient manufacturing and use of renewable energy in factories are trending in the industry.
Another growing trend is adding functional enhancements to wipes and nonwoven materials. This means car wipes are not just plain cloths – they might be treated with cleaning agents, anti-microbial coatings, or other functional finishes at the factory. For instance, a car wipe could come pre-moistened with a dashboard protectant, or a polishing wipe might have embedded micro-abrasives for better cleaning. From the material standpoint, nonwoven fabrics can be engineered to have properties like flame retardancy, UV resistance, or anti-bacterial functionality through specialty fiber additives or finishing processes. In technical sectors, we even see nonwovens being part of “smart” materials (for example, as carriers for sensors or conductive layers), though such applications are still emerging.
On the production side, the concept of “smart manufacturing” and Industry 4.0 has entered the nonwovens industry. Manufacturers of nonwoven machinery and wipes are adopting advanced automation and digital monitoring to improve efficiency and quality. Modern production lines use sensors and IoT (Internet of Things) technology to continuously monitor fiber feed, web uniformity, needle wear, and other parameters. This results in more consistent product quality and less downtime. For example, if a part of the needle loom is experiencing a fault, the system can alert operators immediately or even adjust processes automatically. Such automation and data-driven control helps reduce operating costs and increase output, which is important as global demand rises. It also allows for more flexibility – quick changeovers to produce different types of wipes on the same line, which can help manufacturers respond to market needs (like suddenly producing more disinfectant wipes during a health crisis).
Lastly, the global demand for car wipes/nonwovens is not just about quantity but also about geography. North America, Europe, and Asia-Pacific are all large markets for nonwoven products, with Asia (particularly China) growing rapidly both as a producer and consumer. The automotive industry’s growth in developing countries means more use of nonwoven components in cars (from interior fabrics to filtration), indirectly boosting the car wipes segment as well. Additionally, consumer awareness of cleanliness and convenience in countries with growing middle classes leads to higher uptake of disposable wipes for car care and home use.
In summary, the car wipes industry is evolving with a keen eye on sustainability and innovation. The combination of high functionality, low cost, and adaptability ensures that nonwoven wipes remain in demand. At the same time, manufacturers and users are increasingly mindful of making these products greener and smarter. Moving forward, we can expect car wipes to become even more environmentally friendly (perhaps fully biodegradable) and to incorporate advanced features, all while meeting the global appetite for efficient cleaning solutions. The humble nonwoven wipe has come a long way from a simple piece of fabric – it sits at the intersection of materials science, environmental responsibility, and everyday practicality, a true example of an industrial product that impacts our daily lives in many unseen ways.
Elbert Zhao
Founder, ELBERT Wipes Solutions
📧[email protected] | 🌐 www.elbertwipes.com
8 production lines | 22 processing lines | OEKO-TEX certified | Walmart-approved supplier