Needle Punched Nonwoven Jumbo Roll
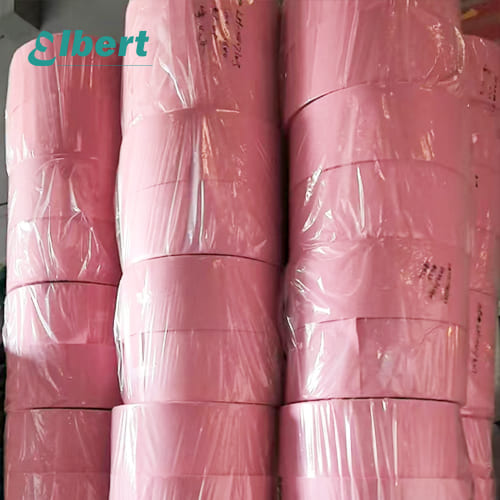
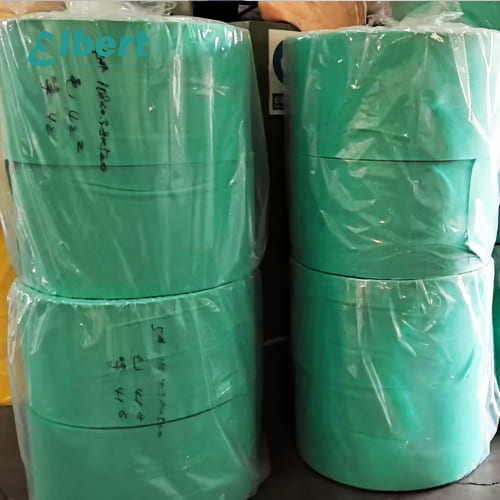
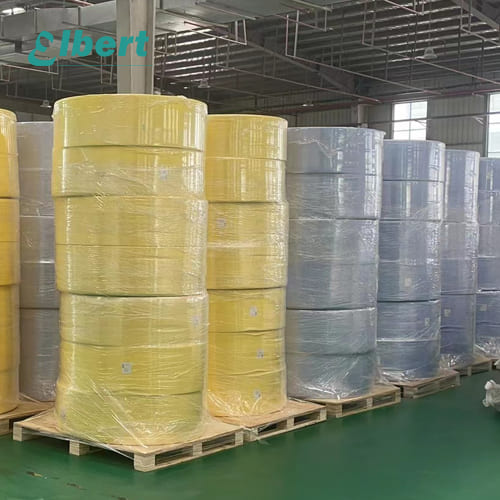
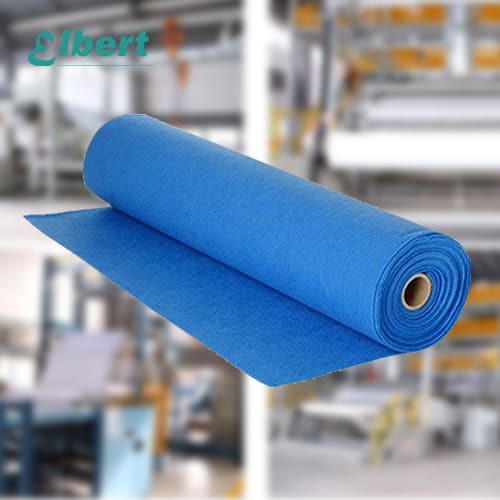
My name is Elbert Zhao, and I represent ELBERT from China. Our company focuses on nonwoven cleaning wipes, functional wet wipes, and microfiber towels. We support B2B business models and offer OEM/ODM customization services. Today, I share with you an in-depth look at the needle punched nonwoven jumbo roll. I will talk about its manufacturing process, main features, applications, and market trends. This article uses simple and direct language to help you understand the topic clearly.
1. Introduction
Needle punched nonwoven jumbo roll is a type of fabric made by entangling fibers with barbed needles. It is used in many areas. This fabric is popular because it has high strength, good breathability, and can be customized. In this article, I will discuss the manufacturing process, product features, application areas, other potential uses, and both advantages and limitations. I will also talk about market trends and the future of the needle punched nonwoven jumbo roll.
At ELBERT, we believe that a product must be strong, safe, and made with care. Our aim is to provide high-quality nonwoven products that meet the needs of customers worldwide. You can learn more about our work on our website: www.elbertwipes.com.
2. Manufacturing Process
The creation of a needle punched nonwoven jumbo roll involves several clear steps. These steps ensure that the final product is strong and reliable. The process can be broken down into the following stages:
2.1 Fiber Preparation
-
Raw Material Selection: Natural or synthetic fibers are chosen based on the product needs. The choice of fiber affects strength and breathability.
-
Cleaning and Sorting: Fibers are cleaned to remove any impurities. They are then sorted by length and type.
-
Carding: The fibers are combed to align them. This step makes the fibers easier to form into a web.
2.2 Fiber Web Formation
-
Laydown Process: Fibers are laid on a moving belt to create a loose web. The fibers are spread evenly over the belt.
-
Bonding: Sometimes a bonding agent is added. This agent helps the fibers stick together before the needle punching process begins.
2.3 Needle Punching Process
-
Needle Penetration: Barbed needles move up and down, entangling the fibers. Each needle pushes through the web, catching fibers and linking them together.
-
Repetition: This needle action is repeated many times. The process creates a dense and stable fabric.
-
Pattern Control: The density and pattern of needle penetration can be controlled. This customization improves strength and appearance.
2.4 Post-Treatment
-
Heat Treatment: The fabric may be exposed to heat. This helps to set the fiber bonds.
-
Calendering: The material can be pressed to improve texture and uniformity.
-
Finishing: Special coatings or treatments may be applied. They help to enhance the final product’s properties like water resistance or softness.
A simple table summarizes the manufacturing process:
Stage | Key Actions | Purpose |
---|---|---|
Fiber Preparation | Cleaning, sorting, and carding | Align fibers and remove impurities |
Fiber Web Formation | Laydown and bonding | Form an even fiber web |
Needle Punching Process | Needling the web repeatedly | Entangle fibers to create strength |
Post-Treatment | Heat treatment, calendering, finishing | Set bonds and enhance properties |
This table shows the clear steps that make up the production process of needle punched nonwoven jumbo roll.
3. Main Features
The needle punched nonwoven jumbo roll has many qualities that set it apart from other nonwoven materials. Here are the key features:
3.1 High Strength
The fabric is made by entangling fibers with needles. This process gives the fabric excellent strength. It can bear stress and load. The product is ideal for applications that require durability.
3.2 Good Breathability
The structure of the fabric allows air to pass through easily. This makes it suitable for products that need to breathe, such as filters and insulation materials.
3.3 Customizable
Manufacturers can adjust many parameters. They can change fiber types, needle patterns, and post-treatment options. This makes the product very flexible. Customers can get a roll that suits their specific needs.
3.4 Environmental Friendliness
The needle punching process does not need extra chemicals. The process uses less energy compared to some traditional fabric production methods. Many manufacturers now use eco-friendly fibers such as plant-based materials.
3.5 Economic Efficiency
The production process is simple and robust. It can be done in high volumes. This efficiency helps to reduce production costs. It makes the product a cost-effective option for many industries.
A chart shows the main features of the needle punched nonwoven jumbo roll:
Feature | Benefit |
---|---|
High Strength | Durable use |
Good Breathability | Airflow, comfort |
Customizable | Tailored to needs |
Eco-Friendly | Low environmental impact |
Economic Efficiency | Cost-effective production |
4. Application Areas
Needle punched nonwoven jumbo roll is used in many fields. The product is versatile and fits a wide range of applications. Here are some main areas:
4.1 Filter Materials
The fabric’s structure makes it a good filter medium. It traps particles while allowing air or liquids to pass. This is useful in air filters, water filters, and even oil filters. Many companies use it in industrial and household filtration systems.
4.2 Geotextiles
Geotextiles help in soil stabilization and drainage. The needle punched fabric is strong and durable. It is used in road construction, erosion control, and drainage applications. These geotextiles can support long-term infrastructure projects.
4.3 Automotive Interiors
The fabric can be used in car interiors. It is used for seat padding, insulation, and sound dampening. The product meets strict safety and quality standards. Its strength and durability add value to automotive parts.
4.4 Home Furnishings
Needle punched nonwoven jumbo roll is used in making home textiles. It is found in products like curtains, cushions, and upholstery. Its good breathability and strength make it a useful choice for daily use.
4.5 Industrial Materials
The material is used in many industrial applications. It is found in packaging materials and insulating layers. Its strength and resilience help protect goods during shipping and storage.
4.6 Insulation Materials
Because of its good air flow and stable structure, the material is also used in insulation. It can help regulate temperature in buildings and other structures.
4.7 Packaging Materials
The fabric is used for industrial packaging. It is strong and can absorb shocks. This helps to keep products safe during transportation.
The following table presents the application areas and their key benefits:
Application Area | Key Benefit | Example Use Case |
---|---|---|
Filter Materials | Particle trapping with airflow | Air and water filters |
Geotextiles | Soil stabilization, drainage | Road construction, erosion control |
Automotive Interiors | Durability, noise reduction | Car seats, insulation panels |
Home Furnishings | Breathability and strength | Upholstery, curtains, cushions |
Industrial Materials | Protection and shock absorption | Packaging, insulation layers |
Insulation Materials | Temperature regulation | Building insulation |
Packaging Materials | Robust and safe packaging | Industrial shipping packaging |
5. Other Application Fields
In addition to the main uses, needle punched nonwoven jumbo roll is finding new areas of application. These include:
5.1 Agricultural Covers
Farmers use nonwoven fabrics for mulching and soil protection. These covers help retain soil moisture and reduce weed growth. The fabric is strong enough to last a full season.
5.2 Medical Products
The fabric can be used in some medical applications. It is used in wound dressings and protective garments. Its high strength and customizable features are valuable in health care products.
6. Advantages and Limitations
Every product has its pros and cons. Here are the main points for needle punched nonwoven jumbo roll.
6.1 Advantages
-
Multi-functionality: It works in many areas. It can be used in filters, insulation, and packaging.
-
Durability: The fabric has high strength. It stands up to stress and heavy use.
-
Eco-Friendly: The production process uses fewer chemicals. Many fibers are from renewable sources.
-
Customization: Customers can choose fiber type, density, and post-treatment. This allows products to be tailor-made.
6.2 Limitations
-
Hard Hand Feel: The fabric can feel stiff. This can be an issue in applications where softness is required.
-
Higher Production Cost: The process uses many needles and may require more energy. This can raise the cost when compared to other nonwoven processes.
A side-by-side view in a table helps to understand these points:
Aspect | Advantage | Limitation |
---|---|---|
Functionality | Multi-use in various industries | May not be ideal for soft touch |
Durability | High strength and lasting | May add cost to production |
Environmental | Fewer chemicals and eco-friendly | Cost and energy in needle punching |
Customization | Tailor-made options available | Limited by raw material choices |
7. Market and Development Trends
The market for needle punched nonwoven jumbo roll is growing. Here, I discuss some trends and future outlook.
7.1 Functionality Improvement
Many companies work to improve the product’s functions. They focus on better fiber bonding and new post-treatments. These improvements increase strength and durability. Innovation is key to meeting industry demands.
7.2 Eco-Friendly Material Application
The world now values products that do less harm to nature. Manufacturers use plant fibers like viscose, wood pulp, and corn fiber. These fibers make the product more eco-friendly. Many markets, especially in Europe and North America, favor sustainable materials.
7.3 Intelligent Manufacturing
New technologies help to make the process more efficient. Smart machines can adjust needle density and speed. This brings lower costs and better quality. Intelligent manufacturing is a trend seen in many industries.
7.4 Market Expansion
The demand for nonwoven products is rising in many parts of the world. There is growth in areas such as Asia, Africa, and South America. The expansion is due to rising industrial needs and increased consumer awareness of eco-friendly products.
A simple bar chart can show these trends in a clear way:
Trend | Growth Level (Scale 1-5) |
---|---|
Functionality | 4 |
Eco-friendly | 5 |
Intelligent Mfg. | 4 |
Market Expansion | 5 |
The chart shows that eco-friendly materials and market expansion have a high growth level. Functionality and intelligent manufacturing are also on the rise.
8. Conclusion
Needle punched nonwoven jumbo roll is a product with many uses and strong qualities. It is made using a process that includes fiber preparation, web formation, needle punching, and post-treatment. The final product is strong, breathable, and customizable. Its applications range from filters and geotextiles to automotive interiors and insulation. The product also shows promise in agricultural and medical fields.
At ELBERT, we use our experience to produce high-quality nonwoven products. We are proud of our strong production technology and advanced equipment. We work with well-known brands in North America, Europe, and beyond. Our focus is on eco-friendly materials and fast delivery. Our products have been tested and certified by quality assurance teams. We meet standards such as ISO, OEKO-TEX, and SGS.
Our business model is based on trust and quality. We welcome partnerships with distributors, brand owners, and OEM service providers. We offer flexible customization options in terms of color, size, print, and packaging. Our pricing model is designed to offer competitive rates without lowering quality. We maintain close ties with major ports and logistics partners. This helps us deliver on time, every time.
In summary, needle punched nonwoven jumbo roll stands as a strong, versatile, and eco-friendly material that meets modern market demands. Its simple manufacturing process and diverse application areas make it a valuable asset for many industries. We at ELBERT continue to innovate and improve our products. We are dedicated to quality and customer satisfaction. I invite you to learn more about our offerings at www.elbertwipes.com or to contact me directly at [email protected].
This article shows how clear, simple language can explain a complex process. It draws on both academic research and practical insights. The points discussed here are supported by industry standards and external examples. For further reading on nonwoven technology, you may refer to trusted sources like Technical Nonwovens and Nonwovens Industry.
I hope this article has given you a solid overview of needle punched nonwoven jumbo roll. It is my aim to share knowledge and support informed decisions in this dynamic industry. Thank you for your time and interest.
Elbert Zhao
Founder, ELBERT Wipes Solutions
📧[email protected] | 🌐 www.elbertwipes.com
8 production lines | 22 processing lines | OEKO-TEX certified | Walmart-approved supplier